目前,我國在役鐵路貨車約70萬輛,其中敞車約占總量的70%[1]。Q450NQR1因具有強度高、耐蝕性好的特點,成為現役鐵路敞車的主要用鋼,廣泛應用于C70敞車上[2,3],為我國煤炭運輸做出了巨大貢獻。針對中車提出對鐵路敞車用鋼輕量化的目標,450 MPa級高強耐候鋼已經足夠滿足80 t鐵路敞車體強度的設計要求,這就要求新型鐵路敞車用鋼在兼具低成本的同時,具有更優異的耐腐蝕性能[4,5]。
文獻[6-9]表明珠光體組織是與夾雜物相似的腐蝕起源點,珠光體誘發局部腐蝕表現為:珠光體中滲碳體與鐵素體之間的電位差引發電偶腐蝕,對材料耐蝕性是不利的。為避免珠光體組織對實驗鋼耐蝕性的不利影響,本文在實驗室條件下制備了一種鐵路敞車用經濟型450 MPa級高強耐候鋼,后通過控軋控冷,獲得了3種不同珠光體含量的高強耐候鋼,旨在研究顯微組織對高強耐候鋼耐大氣腐蝕性能的影響,為鐵路敞車用經濟型高強耐候鋼的開發提供參考。
1 實驗方法
在實驗室條件下制備了一種鐵路敞車用經濟型450 MPa級高強耐候鋼,綜合考慮其力學性能、焊接性能和耐蝕性能的要求,采用低Mn、S和高Ti的化學成分設計,并復合添加耐蝕元素Cr、Ni、Cu。實驗鋼與對比鋼Q345B的化學成分如表1所示。
表1 實驗材料化學成分
在實驗室條件下,將實驗鋼坯料加工成220 mm×220 mm×50 mm的方坯,最終軋制為厚度7 mm的熱軋態鋼板。通過控軋控冷獲得3種不同顯微組織的實驗鋼,力學性能如表2所示。
表2 實驗鋼的力學性能
周浸腐蝕實驗依據TB/T 2375-1993進行,實驗材料是Q345B鋼及1#、2#、3#實驗鋼。尺寸為60 mm×40 mm×4 mm,每種材料取5個平行試樣;實驗前依次用丙酮、無水乙醇除去表面油污,在干燥箱中干燥24 h 后稱重。腐蝕液為0.01 mol/L的NaHSO3溶液,溶液溫度為45 ℃,濕度70%RH,實驗時間為72 h。
腐蝕產物的去除按照GB/T 16545-2015,緩蝕劑配置為:500 mL鹽酸+500 mL蒸餾水+3.5 g六次甲基四胺。通過超聲波清洗儀去除試樣表面腐蝕產物,酸洗后用清水沖凈,再依次用丙酮和無水乙醇浸泡,取出后立即用熱風吹干,放入干燥器中保存24 h后對試樣進行稱量。腐蝕失重率w如下:
式中,w為腐蝕失重率,g/(m2·h);g0和g1為試樣腐蝕前后質量,g;a、b和c分別為試樣長度、寬度和厚度,mm;t為實驗時間,h。
實驗結束后,采用Sigma 500熱場發射掃描電子顯微鏡 (SEM) 對實驗鋼腐蝕后各區域進行微觀形貌觀察,并利用其自帶的能譜分析儀 (EDS) 分析腐蝕產物的化學成分。采用PARSTAT 2273電化學工作站測定3種組織實驗鋼的動電位極化曲線。
2 結果和分析
2.1 實驗鋼顯微組織分析
不同工藝下實驗鋼的金相組織如圖1所示,實驗鋼1#組織為鐵素體 (F)+珠光體 (P),實驗鋼2#、3#的組織為鐵素體 (F)+貝氏體 (B)+珠光體 (P),但構成比例不同,分別為85%F+15%P、81%F+14%B+5%P、82%F+16%B+2%P (以下分別簡稱為15%P、5%P、2%P)。
圖1 3種實驗鋼的金相組織
2.2 組織對實驗鋼耐蝕性的影響分析
3種組織實驗鋼與對比鋼Q345B的腐蝕速率結果如圖2所示。可見實驗鋼的腐蝕速率隨著珠光體占比的降低而降低,可見在周浸腐蝕條件下,珠光體組織對材料的耐大氣腐蝕性能存在不利影響。
圖2 實驗鋼腐蝕失重率
3種組織實驗鋼與對比鋼Q345B在周浸腐蝕試驗后的宏觀腐蝕形貌如圖3所示。對比鋼Q345B呈棕黃色,表面覆蓋一層疏松銹層,與基體結合力差,容易剝落;隨著腐蝕時間延長,銹層逐漸變成褐色;15%P鋼呈灰綠色,表面平整,僅在懸掛試樣的孔洞附近存在少量疏松銹層;5%P鋼與2%P鋼腐蝕形貌相似,顏色呈深綠色,懸掛試樣的孔洞附近依然存在少量疏松銹層。實驗鋼總體上呈現平整的腐蝕形貌,表面腐蝕產物分布均勻,附著緊密,對基體具有更好的保護作用。
圖3 3種實驗鋼及對比鋼周浸腐蝕實驗后的腐蝕形貌
圖4為3種實驗鋼與對比鋼Q345B鋼在周浸腐蝕實驗后的腐蝕產物微觀形貌。可見Q345B鋼表面腐蝕產物疏松,出現明顯的腐蝕層開裂形貌,局部腐蝕產物已經脫落。15%P鋼可見內銹層與外銹層的分界線,外銹層已經大量脫落,內銹層致密均勻;5%P鋼外銹層基本脫落完成,內銹層腐蝕產物出現局部團聚形貌;2%P鋼表面腐蝕產物呈土丘狀,腐蝕產物上又生成了更細小的顆粒狀腐蝕產物,均勻而致密,有效隔絕了腐蝕介質向基體內的滲透,降低了酸性介質對基體的腐蝕。由此可見,隨著P組織含量的降低,實驗鋼的整體耐腐蝕性較好,腐蝕方式以均勻腐蝕為主,較快生成了致密內銹層,腐蝕產物緊緊地依附在基體表面,沒有明顯的坑洞和裂紋。
圖4 試樣表面腐蝕形貌的SEM像
2.3 實驗鋼動電位極化曲線分析
3種實驗鋼的動電位極化曲線如圖5所示,其對應的自腐蝕電位 (Ecorr / V) 和電流密度 (Icorr / μA·cm-2) 分別為-0.67,-0.65,-0.61及25.0,28.1,35.2。2%P鋼的極化曲線在最上方,表明其腐蝕電位最高。15%P鋼極化曲線圖形位于最下方,腐蝕電位最低。從表中可以看出:試樣的腐蝕電位排序與腐蝕電流結果相反,該現象表明低P組織鋼在腐蝕初期,發生陽極溶解的速度最快。這是因為在鋼基體表面致密銹層形成之前,腐蝕行為主要取決于鋼基體內各部分的電極電位之差[10]。珠光體為鐵素體與滲碳體的機械混合物,晶內鐵素體和滲碳體交錯,兩者電位存在明顯的差異[11],在液膜下形成的大量微電池加速了珠光體的腐蝕。在電化學腐蝕中,“大陰極小陽極”會使腐蝕加劇,因此2%P鋼在腐蝕初期即致密銹層形成之前會迅速腐蝕。
圖5 實驗鋼的動電位極化曲線
2.4 實驗鋼銹層結構與元素分布分析
為進一步分析不同P組織含量的實驗鋼腐蝕差異性,選取15%P鋼與2%P鋼,對其銹層結構及元素分布進行觀察,如圖6所示。可見15%P鋼外銹層已經脫落,裂紋延伸至整個內銹層,內銹層與基體連接的局部出現了應力開裂形貌。腐蝕坑深度約32~37 μm,寬度約40~74 μm。Cr在銹層表面與裂縫處都出現了富集,Cu則在銹層表面與腐蝕坑內出現了明顯富集,而S在腐蝕的過程中逐步侵蝕至基體內,并在腐蝕坑內大量富集。
圖6 15%P和2%P鋼試樣的截面腐蝕形貌
2%P鋼銹層結構與15%P鋼相似,銹層出現開裂,但外銹層并未脫落,可見2%P鋼銹層厚度要比15%P鋼小很多。2%P鋼腐蝕坑尺寸明顯較15%P鋼小,深度約19~32 μm,寬度約24~34 μm。Cr在銹層表面與裂縫處都出現了富集。與15%P鋼顯著不同的是,S僅擴散至銹層裂縫處,腐蝕坑內S含量很少,而基體內基本消失不見,Cu富集位置與S富集位置基體一致,可見Cu對S向基體內的侵蝕起到顯著的抑制作用。
Cu是提高材料耐蝕性[12-15]最有效的元素之一,為進一步研究Cu在抑制腐蝕過程中起到的作用與存在狀態,對銹層中Cu的存在狀態與含量進行了測定,結果見圖7所示。可見15%P鋼銹層表面存在許多小而彌散分布的多面體晶石物相,這種物相多分布于完整的銹層上,而銹層開裂處少有分布,經EDS分析為富Cu相。這表明Cu在內銹層上形核,并對內銹層起到“錨固”作用,改善銹層結構,防止銹層開裂。
圖7 內銹層腐蝕形貌的SEM像及EDS結果
2%P鋼富Cu相呈團聚狀,與15%P鋼不同的是,Cu在內銹層形核后,逐漸長大,數量更多,尺寸也更大,對腐蝕介質的隔絕作用,效果更為顯著。同時富Cu相上出現了更多更細小的彌散富Cu相,揭示了富Cu的形核與長大過程。
3 結論
(1) 通過控軋控冷獲得3種不同珠光體含量的高強耐候鋼,周浸腐蝕實驗結果表明,珠光體組織含量越低,銹層越致密,耐蝕性越好。
(2) 動電位極化曲線結果與周浸腐蝕實驗結果一致,即珠光體含量越低,腐蝕越難發生,但在腐蝕初期即致密銹層形成之前,低珠光體組織會率先發生陽極溶解。
(3) Cu在銹層與腐蝕坑內富集,有效抑制了S向基體內侵蝕,隔絕了酸性腐蝕介質,減緩了腐蝕的進程。Cu在內銹層上形核并長大,對內銹層起到“錨固”作用,抑制了其開裂進程。
免責聲明:本網站所轉載的文字、圖片與視頻資料版權歸原創作者所有,如果涉及侵權,請第一時間聯系本網刪除。
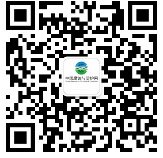
官方微信
《中國腐蝕與防護網電子期刊》征訂啟事
- 投稿聯系:編輯部
- 電話:010-62316606-806
- 郵箱:fsfhzy666@163.com
- 中國腐蝕與防護網官方QQ群:140808414