引言
軸承是承受載荷、傳遞運動的關鍵機器零件。現代設備制造業不斷增加功率密度帶來的挑戰,對軸承的承載能力和可靠性提出了更高的要求。
現今,軸承滾動接觸疲勞造成的軸承失效一般很少發生,并且滾動軸承最終實現的使用壽命通常遠遠超出計算的額定壽命。然而,在特定應用中的軸承會過早失效,其使用壽命只占計算的額定壽命的5%至10%。軸承過早失效發生的時間間隔通常很短,即與正常滾動接觸疲勞相比,其呈現高斜率威布爾分布 (圖1)。
圖1 威布爾軸承失效分布,紅色斜線:典型的早期失效情況;藍色斜線:正常接觸疲勞測試的斜率
許多早期失效的軸承都有一個典型的特征——出現帶“白蝕形貌”的大面積表面下裂紋網絡的存在,這通常被稱為白蝕裂紋(WEC)(圖2)。這種裂紋通常會擴散至表面,導致滾道剝落,該現象常見于風力發電機齒輪箱、汽車傳動系統、交流發電機與周邊輔助設備、造紙廠和船舶推進系統等應用領域的返回產品中。一些典型的例子如圖3所示。15年來,業內對這種失效的根本原因進行了廣泛的討論,基于從不同角度進行的檢查提出了各種假設。對各種假設進行的綜合評估和分析列在中。過去數十年,人們從不同的角度研究軸承過早失效的問題,因此對該問題的特定方面有了更多的了解。然而,在軸承失效分析方面,主要參與者依然對根本原因和失效機制缺乏共識。
圖2 典型的大范圍白蝕裂紋網絡;大型球面滾子軸承。
圖3: 來自以下應用領域的幾個軸承過早失效的典型實例(a)造紙機、(b)壓縮機、(c)風力發電機齒輪箱的低速段和(d)風力發電機齒輪箱的高速段。
過去四年間(本文發表于2018年),SKF更深入地調查和研究白蝕裂紋現象,旨在理清白蝕裂紋在軸承滾動接觸疲勞和加速疲勞(軸承過早剝落)過程中發揮的作用。雖然材料科學界仍在討論這個問題,但SKF的研究發現表明:白蝕裂紋發生在失效鏈的末端,是過早失效軸承的裂紋網絡產生的自然結果。SKF認為,白蝕裂紋是疲勞失效的一種征兆,而非根源。本文闡述了SKF專家對過早失效和白蝕裂紋的多數共識看法。此外,還提出了白蝕裂紋的定義,討論了其成因,并提出了導致白蝕裂紋的所有失效原因機制。
白蝕裂紋的定義
白蝕裂紋是軸承鋼的微觀結構中的裂紋,它們被白蝕區所點綴。白蝕是指拋光和浸蝕鋼樣時發現其微觀結構已經發生改變,呈現白色外觀。受影響的區域由超細的納米重結晶無碳化物鐵素體或具有非常細微的碳化物顆粒分布的鐵素體組成。
白蝕區是由裂紋面在重復滾動中因摩擦造成的無定形化而形成的。由于這些區域對腐蝕反應不敏感,因此在光學顯微鏡下呈現白色。裂紋周圍的白蝕區比附近未受影響的微觀結構硬10%到50%。
形成原因
3.1滾動接觸疲勞中的白蝕裂紋
眾所周知,小型、重載的長期運轉軸承在失效(非常高的循環疲勞)之前會經歷幾個疲勞階段。
第一階段是振動硬化階段,會導致微塑性變形、加工硬化,并最終積累殘余應力。在振動硬化狀態,軸承表面也可能發生一些微塑性變形,變形部位的粗糙表面會變平。
在振動硬化后,開始進入影響軸承壽命的主要環節,其特征是微觀結構逐漸改變。在此階段,碳化物分布由于微塑性變形而發生變化。此外,殘余的奧氏體也可能逐漸減少,所有微觀結構變化都伴隨著殘余應力的積累。
在軸承滾動接觸疲勞的末期階段,發現有暗蝕區(DER)且伴有白蝕、低角度帶(LAB)和高角度帶(HAB)(圖4左)。雖然高角度帶和低角度帶也都是白蝕,但相比軸承早期失效中形成的不規則白蝕裂紋,它們有不同的外觀。由此可以得出結論:不規則白蝕裂紋的形成不是滾動接觸疲勞一部分。不過,這些白蝕區的微觀結構在晶體結構上與過早失效中觀察到的白蝕區并無很大區別。
對于大中型軸承來說,上面列出的影響出現的方式,并不一定與小型重載軸承相同。與其他機械部件一樣,這些軸承典型的失效原因在于其最薄弱的環節受損(例如,夾雜物和孔隙等材料結構中預先存在的缺陷)。如ISO/TR 1281-2:2008所述,當軸承的平均直徑大于100毫米時,其疲勞極限會下降。此外,若比較接觸應力對較小軸承和較大軸承的影響,受影響的應力體積在較大軸承中會增加,正如薄弱環節所產生的負面影響。其中一個例子是夾雜物,它們在所有軸承鋼中天然存在。另外一個發揮作用的因素是接觸應力本身;在圖4中給出的例子中,在低角度帶和高角度帶產生的地方,接觸應力相對較高 (>3.2 GPa)。在許多大中型軸承中,施加的接觸應力遠低于3GPa,這意味著疲勞載荷處于另一種狀態,這導致全局損傷較少,更多的是非金屬夾雜物附近的局部損傷。
早在20世紀60年代,就有報告指出,在滾動接觸疲勞軸承中有出現白蝕裂紋和暗蝕圖案。到了80年代,SKF內部也報告了這一點。對于過早失效的大中型軸承的后期研究(通過高加速壽命測試或標準耐久測試)已經證實,大范圍的不規則白蝕裂紋網絡的出現是軸承滾動接觸疲勞的自然附帶產生的結果(圖4右)。
圖4:左:深溝球軸承中的暗蝕區、低角度帶和高角度帶;右:大型圓錐滾子軸承耐久測試中出現的白蝕裂紋。
3.2加速疲勞中的白蝕裂紋(過早剝落)
可以通過在剝落開始之前發生不同事件所需的時間,來區分過早剝落(行業里通常被解釋為白蝕裂紋失效)和正常的滾動接觸疲勞(圖5)。此外,與耐久性測試或正常滾動接觸疲勞相比,軸承失效分析顯示:過早失效通常和幾個位置/區域的裂紋起始點有關。
圖5 引起白蝕裂紋發展的簡化事件鏈。
軸承鋼出現裂紋的原因可能不同,在環境原因造成應力較高或強度降低的情況下,裂紋會加速發展(圖6)。軸承所受的應力可能高于預期。這種情況的例子如下:
意想不到的動態的或溫度的影響可能引起短期重載,導致結構變形的大預緊力、邊緣載荷等。
軸承材料中的結構應力(例如,由形狀偏差、不對中或其他因素引起)會增加材料中的應力。
惡劣的摩擦學接觸條件(例如油膜厚度太薄和/或滑動條件),加上特定的潤滑劑,也可能導致滾道上的應力增加。
一些可能產生氫的環境因素會對軸承的材料強度造成不利影響。這些可能包括:水污染、腐蝕和雜散電流。在這些情況下,正常載荷條件就可能導致過早失效。
SKF通過專門的軸承測試,驗證了加速疲勞的成因,它們都與應力較高和材料強度較低有關。
圖6 滾動軸承中白蝕裂紋的出現(簡化)。
一旦裂紋形核(有時伴隨著暗蝕區的出現),裂紋面[18-22]上的摩擦過程會導致材料從裂紋的一側轉移到另一側。這將導致曲折裂紋的出現,并在裂紋的接收側積累白蝕顯微組織。
白蝕區的發展也取決于次表面裂紋的走向,這可能與起作用的內力和形變模式有關。這就是為什么在水平方向的裂紋(平行于滾道)中白蝕區更加常見,而垂直方向的裂紋部分常常較少出現白蝕區跡象(圖7)。另外,白蝕區的產生還取決于裂紋面之間的間隙和應力循環的數量,以及材料中的內部應力狀態。
圖7 SKF內部測試軸承(滲氫軸承測試)的表面下裂紋中的白蝕圖案。
3.3由于應力增加導致白蝕裂紋出現的例子
圖8、9和10顯示了與應力相關的白蝕裂紋開始出現的兩個例子。圖8和圖9所示的結果是與某個軸承測試臺有關,它被設計成通過波紋人為地將結構應力或結構變形引入軸承座,從而讓軸承內圈出現局部拉伸應力。該測試采用某圓柱滾子軸承,其內圈(內徑為220毫米)以正常配合安裝在五葉波紋套管上,該套管以過盈配合安裝在軸上。通過硬車制成的波紋套管,將在內圈的軌道表面附近產生五個拉伸應力約為205MPa的區域。測試軸承是一種改進的雙列圓柱滾子軸承,在內圈的中心部分配備有一排8個滾子,而不是兩排24個滾子,以適應測試臺的測試能力,從而實現所需的接觸應力(圖8)。軸承材料為SAE 52100(100Cr6)鋼,軸承的金相組織為回火馬氏體,且殘余奧氏體含量多達7%(體積分數),硬度為62 HRC。
這些軸承在最大赫茲接觸壓力1.8 GPa、kappa值約為2的條件下進行了測試。軸承測試直至失效為止。
圖8 過早失效的軸承,內圈滾道有軸向裂紋。
一個軸承在五葉波紋套管上經過1150小時(對應于6.35×108個應力循環)后失效,滾道上出現一個可見的軸向裂紋。第二個軸承在1570小時(對應于8.67×108個應力循環)后失效,出現兩個可見的軸向裂紋。軸向裂紋的位置在圓周方向上與其中一個波峰處重合,波峰處存在拉伸應力區。
應該注意的是,先前已在相同的條件下使用標準軸配合(沒有人為引入的波紋)測試了四個同樣的軸承,測試大約進行了2,200小時(對應于1.21×109次應力循環)后暫停,在此之前這四個軸承沒有一個失效。在后期分析過程中未發現表面裂紋和次表面白蝕裂紋。
后期分析包括使用超聲波測試(UST)和滲透法測試的無損檢測(NDT)、套圈圓度測量、斷口分析和顯微鏡下金相檢查。
如圖9所示,在打開裂紋的樣品上制備橫截面。在腐蝕后可以觀察到,主裂紋的一部分在光學顯微鏡下顯現白色,而在表面下方約500微米深度處裂紋分叉。分叉裂紋也是沿著與滾道平行的方向擴散的白蝕裂紋,與主裂紋相距約400微米。分叉裂紋的放大圖(圖9b、c和d)證實了裂紋相互連接、在表面下形成網狀白蝕裂紋的理論。在與波紋套管軸波峰處相對應的另外兩個圓周位置,也制備橫截面。雖然在表面上沒有觀察到表面裂紋,但在這些區域的表面下發現多個白蝕裂紋,這些區域在測試期間存在由波紋引起的拉伸應力。
圖9 在光鏡下顯示的軸向裂紋的平行截面的白蝕裂紋,以及三個指示區域的放大圖像。主裂紋的一部分和分叉裂紋伴隨有白蝕區。(b)、(c)和(d)中的照片分別是(a)中由數字1-3表示的放大區域。
圖10所示是23024球面滾子軸承在短期重載測試下的結果。
圖10:由短期重載引起的23024軸承外圈中的表面下大范圍白蝕裂紋網絡。
在短期重載期間,軸承在良好的潤滑條件下(kappa約為3.5)承受3GPa以上的接觸應力達15分鐘左右。
將已經承受短期重載的軸承安裝在徑向測試臺上。然后,在接觸應力1.7GPa和Kappa值約為2的潤滑條件下測試。在該條件下,軸承在大約3.3×107次循環后停止承重或者在此之前失效。圖10顯示了外圈的周向切開和進行金相腐蝕的結果。由于外圈承載區剝落,相關軸承在1.9×107次循環后失效。
3.4由于材料強度較低而產生白蝕裂紋的例子
圖7已給出了滲氫軸承的表面下白蝕裂紋的例子。對滲氫和非滲氫的角接觸球軸承以及深溝球軸承的詳細事后分析可參見文獻22。
3.5在摩擦與潤滑劑共同影響下產生白蝕裂紋的例子
在使用FE8測試臺進行潤滑油評估測試時,發現失效的81212圓柱滾子推力軸承中有白蝕裂紋[23]。迄今為止,在混合摩擦和高的運動滑動(不代表徑向滾子軸承)混合測試條件下未得到結論性的結果。到目前為止,FE8測試中的白蝕裂紋主要是由來自表面的疲勞(其中,潤滑劑也起到重要作用)造成的,還是由于氫進入,亦或是二者共同的結果,無法給出最終結論。
圖11 81212軸承滾子的典型失效外觀(左)和墊圈內出現的白蝕裂紋(滾道下84um處的橫截面)(右)
使用鋼對鋼測試系統對81212圓柱滾子推力軸承進行了軸承測試。軸承材料為SAE 52100標準軸承鋼,馬氏體硬化,殘余奧氏體含量小于3%,硬度約為60HRC。這些軸承在中等載荷(最大接觸應力約1.9GPa)和不充分潤滑條件下進行了測試(kappa約為0.3)。
測試采用了不同的潤滑油和混合油。典型失效外觀如圖11所示。
盡管此處沒有詳細說明,但在所有測試中,主要是滾子失效,很少有墊圈失效。測試一直持續到失效(剝落)或最終停止。對于因剝落而失效和發現白蝕裂紋的軸承,假設在任何剝落發生之前,已經產生點綴有白蝕的次表面裂紋。做出這一假設,因為有時在非剝落部件中也發現了次表面裂紋。詳細信息,請參閱文獻15。
討論
上述研究發現解釋了為什么所有類型的工業、所有類型的軸承和所有類型的熱處理(整體淬硬和表面淬硬材料)中都能發現白蝕裂紋,這是因為白蝕裂紋出現在失效鏈的末端,并且是過早失效的軸承中的裂紋網絡產生的自然結果。
要查明軸承過早失效的根本原因,其關鍵不僅在于研究白蝕裂紋,更要找出導致加速疲勞的相關弱化影響(與應力較高或材料強度較低有關)。
一般來說,任何機械部件的失效都是由于其最薄弱環節受損造成的。當局部應力超過局部強度時,就會發生這種情況。過早失效是最薄弱的環節顯著弱化的結果。各種應用中使用的滾動軸承的可靠性符合最弱環節原則。弱點總是存在于材料內或工作接觸面上。如果最弱的環節出現問題,那么軸承就會失效。當潤滑條件不佳或表面粗糙時(例如顆粒壓痕),最弱的環節就最有可能出現在表面上,那么表面損傷(例如表面疲勞或磨損)就會導致軸承失效。在良好潤滑條件下,由于存在材料缺陷(例如,夾雜物和赫茲接觸導致的高剪切應力、軸承失效由于材料預先存在的缺陷引起的裂紋萌生和擴展),那么最薄弱的環節可能就在表面下。
對于滾動軸承來說,最薄弱環節的強度可能與所謂“疲勞極限”的載荷或應力極限有關。如果超過疲勞極限,那么軸承就會失效。當疲勞極限顯著降低時,換句話說,當最薄弱環節的強度顯著降低時,就會發生軸承過早失效。造成早期裂紋產生并加速裂紋擴散,最終導致軸承過早失效的原因,是應力較高或材料強度降低引起的弱化,而不是白蝕裂紋。在不存在弱化現象的情況下,軸承也可能會失效,這是正常滾動接觸疲勞單點剝落的結果,很少或不會產生白蝕裂紋,這是因為當材料壽命結束時,裂紋會迅速擴展[7]。換句話說,沒有時間在裂紋系統內進行材料轉變。隨著弱化程度的增加,軸承可能會過早失效,表現為出現大范圍的白蝕裂紋,因為裂紋系統中的材料有時間在局部從暗蝕區轉變為白蝕區。隨著嚴重程度提高,可能會出現較小范圍的白蝕區點綴的軸向裂紋,甚至會出現沒有白蝕區點綴的斷裂,這是由于裂紋擴展過快所致
建議
每個軸承的過早失效都是獨一無二的。再看圖6,可以看出,過早剝落的原因可能大相徑庭。不存在單一的根本原因,每個失效個案都需要根據相應的運行條件進行檢查。
在將弱化驅動因素分類為“應力較高”和“材料強度較低”的基礎上,可以給出如表1所示的通用建議。該表分別列出了針對應用本身的建議(軸承系統、設計過程)以及進一步提高軸承堅固性的可能性。哪個選項能夠最有效地防止過早失效,取決于具體的應用環境。欲了解更多建議,請聯系SKF應用工程服務部。
表1 避免過早剝落失效的建議
免責聲明:本網站所轉載的文字、圖片與視頻資料版權歸原創作者所有,如果涉及侵權,請第一時間聯系本網刪除。
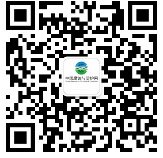
官方微信
《腐蝕與防護網電子期刊》征訂啟事
- 投稿聯系:編輯部
- 電話:010-62316606-806
- 郵箱:fsfhzy666@163.com
- 腐蝕與防護網官方QQ群:140808414