導語
在能源、化工設備、航空航天等工業(yè)領域中,很多機件和零部件是需要在高溫高壓條件下運行,材料在嚴苛條件下其力學性能與常溫下是不同的,會發(fā)生塑性變形和斷裂時效問題,隨著服役溫度和應力的不斷升高,蠕變現象也會越來越明顯,因此研究蠕變現象對高溫服役下的設備器件具有重要意義。今天我們就來講講蠕變性能為何能成為選材和高溫設備設計的重要指標,喜歡的朋友點贊收藏哦~
概述
2)蠕變狹義
指恒定溫度和恒定負荷作用下,材料隨時間產生變形的現象。此處定義便于研究蠕變現象的本質。
3)蠕變斷裂
由于蠕變變形導致的斷裂。
2、蠕變的規(guī)律
蠕變可以發(fā)生在任何溫度,在低溫時蠕變效應不明顯,可以不做考慮。研究表明金屬材料產生蠕變的溫度條件一般為0.3Tm以上,也就是約比溫度大于0.3時,蠕變效應比較明顯。由于不同材料有各自不同的熔點溫度,因此不同材料的蠕變溫度也各不相同。如碳鋼超過300℃,合金鋼超過400℃,需要考慮蠕變效應。
3、蠕變曲線
根據狹義蠕變的定義,在恒定溫度和恒定負荷作用下的蠕變現象可用參量為應變和時間的蠕變曲線來描述,圖1為典型的金屬材料和陶瓷材料的蠕變曲線。
圖1 典型蠕變曲線
蠕變曲線詳解:
oa線段是試樣加載后所引起的瞬時應變e0,又稱起始應變。如果施加的應力超過金屬材料在該溫度下的彈性極限,則e0包括彈性應變和塑性應變兩部分,起始應變不屬于蠕變。從a點開始隨時間增加而產生的應變屬于蠕變,包括隨 時間變化的塑性應變和隨時間變化的彈性應變兩部分。
蠕變曲線上任意一點的斜率表示該點的蠕變速率:
按照蠕變速率的變化,可將蠕變過程分為3個階段:
1)第Ⅰ階段為ab,也成為減速蠕變階段。這一階段隨時間的增長,蠕變速度減小,又稱不穩(wěn)定蠕變,到b點蠕變速度達到最小值。
2)第Ⅱ階段為bc,為恒速蠕變階段,隨著時間的增長蠕變速度幾乎保持不變,又稱為穩(wěn)定蠕變階段,通常作為衡量材料蠕變抗力的依據,材料的最小蠕變速率就是指這一階段的蠕變速度。
3)第Ⅲ階段為cd,為加速蠕變階段,隨著時間的增長,蠕變速度逐漸增大,直至d點產生蠕變斷裂。
圖2為蠕變加載過程的載荷-伸長曲線,起始應變包括起始彈性應變和起始塑性應變,兩者都不屬于時間增長而增加的蠕變變形。
圖2 蠕變加載過程階段的載荷-伸長曲線
圖3 應力和溫度變化對蠕變曲線的影響
當應力較小或溫度較低時,蠕變第Ⅱ階段延長,甚至不出現第Ⅲ階段;
當應力較大或溫度較高時,蠕變第Ⅱ階段縮短甚至消失,該試樣會經過減速蠕變后很快進入第Ⅲ階段而斷裂。
此處延伸展示高分子材料的蠕變曲線,如圖4所示。
圖4 高分子材料蠕變曲線
同樣高分子材料的蠕變曲線也分為三個階段:
1)第Ⅰ階段:AB段為可逆形變階段,為普通的彈性變形,應力與應變成正比;
2)第Ⅱ階段:BC段為推遲的彈性形變階段,也是高彈性變形階段;
3)第Ⅲ階段:CD段為不可逆變形階段,以較小的恒定應變速率產生變形,到后期產生頸縮發(fā)生蠕變斷裂。
4、蠕變曲曲線數學表達式
蠕變曲線數學表達式以解析的方式用來表示蠕變曲線的應變與時間關系,一種簡單通式為:
式中:e-總應變;e0-起始應變;t-蠕變時間;β、K-常數。
等號右邊第一項為瞬時應變,第二項為過渡蠕變引起的應變,第三項式定常蠕變引起的應變,對上面的公式對時間求微分,得到:
式中:n-小于1的正數;
當t很小時,右邊第一項起決定性作用,表示蠕變速度隨時間增長而逐漸減小的過渡狀態(tài)的第Ⅰ階段蠕變;當t增大時,第二項項起主要作用,蠕變速度接近定值,它表示定常狀態(tài)的第Ⅱ階段蠕變。
5、蠕變性能的表征參量
針對高溫下結構選材和設計的需要,蠕變性能采用蠕變極限來表征材料在高溫長時載荷作用下的塑性變形抗力,同時采用延伸率A和斷面收縮率Z作為斷裂時的塑性指標。
蠕變極限是用來衡量蠕變抗力的一個重要參量。蠕變極限又可分為物理蠕變極限和條件蠕變極限。
1)物理蠕變極限
物理蠕變極限是蠕變速度等于零的最大應力,即產生蠕變和不產生蠕變的轉折點的應力。
由于物理蠕變極限需要長時間,且測定蠕變速度接近于零的應力困難,在工程實際應用過程中是允許有蠕變變形的,所以物理蠕變極限在工程應用中意義不大。溫度的高低、應力的大小、時間的長短、測試精度等因素都會顯著地影響蠕變曲線的走勢。因此,為了比較蠕變抗力的大小,工程上常采用條件蠕變極限這一指標來評定。
2)條件蠕變極限
工程上采用兩種辦法表征條件蠕變極限
蠕變速率表征條件蠕變極限
殘余變形率表征蠕變極限
金屬的蠕變變形和斷裂機理
一般在工程上的蠕變速率為,而拉伸變形速率為,熱加工鍛造以及爆炸成型時的蠕變速率為106%/h。相比而言,蠕變變形速度很低,但在高溫低應力的長期作用下,同樣會引起材料組織結構變化,如滑移帶的形成,回復和再結晶,以及微裂紋的形成和擴展,而正是這些組織結構變化導致了蠕變變形和斷裂。
1、蠕變變形機理
蠕變變形主要由位錯滑移 、晶界滑動和擴散三種機制來實現,在不同溫度下三種機制對蠕變變形的貢獻不同。
1)位錯滑移蠕變
滑移在蠕變過程中是重要的變形方式,常溫下,若滑移面上的位錯運動受阻產生堆積,滑移便不能進行,只有在更大的切應力下才能使位錯重新 增殖和運動。在高溫下,位錯可借助于熱激活和空位擴散來克服某些短程障礙,從而使變形不斷產生。
熱激活能能的變形機理有多種,如螺位錯的交滑移、刃位錯的攀移、帶割階位錯的運動等。通過螺位錯的交滑移運動和刃位錯的攀移,可使異號位錯不斷相消,而且也促進位錯的重新組合和排列并形成亞晶界,這就是回復過程。高溫下的回復過程主要是刃位錯的攀移。圖5所示為亞晶界形成示意圖。
圖5 亞晶界形成示意圖
高溫下,由于熱激活,就有可能使滑移面上塞積的位錯進行攀移,形成小角度亞晶界(即高溫回復階段的多邊化),從而導致金屬材料的軟化,使滑移繼續(xù)進行。雖然對蠕變有貢獻的是位錯的滑移,但其進行的速度則受攀移過程所控制。
2)晶界滑動蠕變
常溫下晶界變形不明顯,可以忽略;
高溫下由于晶界強度降低,原子易擴散,形變量增大,促進蠕變;
晶界形變在高溫條件下更顯著,甚至占總蠕變變形量的一半。
晶界變形過程如圖6所示,有A、B、C三個晶粒。
圖6 晶界滑動和遷移示意圖
若A,B晶粒邊界產生滑動(見圖a),則在C晶粒內產生畸變區(qū)(圖中影線區(qū)域),隨后B,C晶粒邊界便在垂直方向上向畸變能較高的C晶粒遷移(見圖b),從而使三晶粒的交會點由1點移到2點。由于C晶粒有畸變區(qū),使A,B晶界繼續(xù)沿原來方向滑動受到阻礙,此時,若A,C晶界產生滑動(見圖c),則進而使A,B晶界又在它的垂直方向進行遷移(見圖d),三晶粒交會點便由2點移到3點。
因此晶界變形是晶界滑動和遷移交替進行的過程。
3)擴散蠕變
擴散蠕變是在高溫條件下空位和間隙原子的移動造成的如圖7所示。是在金屬接近熔點溫度,應力較低的情況下產生的。
圖7 晶粒內部擴散蠕變示意圖
不受外力時,空位移動沒有方向性,不顯示塑性變形;
有外力如拉應力σ作用時,會出現較多空位,晶體內部形成一定的空位濃度;
空位沿實線向兩側流動,原子則沿虛線方向流動,晶體產生伸長的塑性變形,稱為擴散蠕變。
2、蠕變的斷裂機制
蠕變斷裂主要是沿晶斷裂。在裂紋成核和擴展過程中,晶界滑動引起的應力集中與空位擴散起著重要作用。
由于應力和溫度的不同,裂紋成核有下述兩種類型:
1)裂紋成核于三晶粒交會處
在高應力和較低溫度下,晶粒交會處會由于晶界滑動造成應力集中而產生裂紋。圖8所示為幾種晶界滑動方式所對應的晶界交會處產生裂紋的示意圖。這種由晶界滑動所造成的應力集中,若能被晶內變形(例如,在滑動晶界相對的晶粒內引起形變帶)或晶界遷移能以畸變回復的方式使其松弛,則裂紋不易形成,或產生后也不易擴展至斷裂。
圖8 晶粒交會處因晶界滑動產生裂紋示意圖
2)裂紋成核分散于晶界上
在較低應力和較高溫度下,蠕變裂紋常分散在晶界各處,特別易產生在垂直于拉應力方向的晶界上。
這種裂紋成核的過程為:首先由于晶界滑動在晶界的臺階(如第二相質點或滑移帶的交截)處受阻而形成空洞;同時,由于位錯運動和交割產生的大量空位,為減少其表面能而向拉伸應力作用的晶界上遷移。當晶界上有空洞時,空洞便吸收空位而長大,形成裂紋。
3、兩種變形理論對蠕變三階段的描述
1)用裂紋的形核和擴展過程描述蠕變的三個階段
圖9 蠕變裂紋的形核和擴展過程示意圖
蠕變初期晶界滑動影響下在三晶粒交會處形成裂紋核心或在晶界臺階處形成空洞核心;形成的裂紋核心達到一定的尺寸后,在應力和空位流同時作用下會在與拉應力垂直界面長大,形成洞形裂紋,為蠕變第Ⅱ階段;洞形裂紋形成終止于兩個相鄰的三晶粒交匯處的“橫向裂紋段”;相鄰的“橫向裂紋段”通過向傾斜晶界的擴展而形成“曲折裂紋”,裂紋尺寸迅速擴大,蠕變速度迅速增加進入到第Ⅲ階段;蠕變第Ⅲ階段后期,曲折裂紋進一步連接到臨界尺寸產生蠕變斷裂。
2)根據位錯理論及蠕變變形方式描述蠕變的三個階段
蠕變第I階段:以晶內滑移和晶界滑動方式產生變形,在蠕變初期由于晶格畸變能較小,回復軟化過程不太明顯。這一階段的形變強化效應超過回復軟化效應,使蠕變速度不斷降低。
蠕變第Ⅱ階段,晶內變形以位錯滑移和攀移方式交替進行,晶界變形以滑動和遷移方式 交替進行。
蠕變發(fā)展到第Ⅲ階段,由于裂紋迅速擴展,蠕變速度加快。當裂紋達到臨界尺寸便產生 蠕變斷裂。
影響蠕變性能的主要因素
材料的蠕變性能收到金屬內部組織結構、工藝因素和試驗因素等多方面的影響。
1、金屬內部組織結構的影響
1)晶粒強度:晶粒或基體的強度取決于原子間結合力的大小,而提高原子間結合力、使基體強化的方法之一是合金化。
2)晶界強度:提高晶界強度方法如下
采用純凈的爐料與變質劑,減少有害雜質;
加入使晶界原子擴散速度降低的合金元素;
采用熱處理方法使晶粒粗化。
3)第二相的影響
第二相對蠕變有強烈影響。因此,對第二相一般有下列要求:
高度彌散而且均勻分布在晶粒內部,以及與基體共格的,點陣常數與基體相差很大的第二相,其強化效果最大,因為第二相會阻礙位錯的移動。第二相的距離也有一個臨界值,在臨界值下強化效果最好。
擴散能力小,聚集能力差,成分穩(wěn)定,結構復雜,在高溫下長期工作而不起變化的第二相效果最好。
與固溶體沒有互相轉化反應,以及與固溶體間有結晶上的親戚關系的第二相有著高的強化性。
第二相應該是兩種以上,如果其中之一由于不穩(wěn)定進行了聚集,結束了初階段的強化,還可依靠成分變復雜或更穩(wěn)定的其他第二相進行強化。
2、工藝因素的影響
1)熱處理工藝的影響
工作溫度較低時,回復和沉淀過程均不會產生,此時,最好的熱處理是獲得抗拉強度最高的組織狀態(tài),其蠕變抗力也高;
工作溫度較高時,可能有回復和再結晶、相變和沉淀硬化過程的產生,此時熱處理應獲得穩(wěn)定的組織狀態(tài)。
2)冶煉工藝的影響
冶煉質量對強度的影響很深,如鋼中冶煉質量不好,產生非金屬夾雜增多進而導致產生裂紋、疏松、龜裂等問題,均影響強度。
耐熱合金中冶煉質量對強度影響更敏感,對雜 質元素和氣體含量的要求更嚴格。常有雜質除S,P外,還有Pb,Sn,As,Sb,Bi等,其含量即使只有十萬分之幾,也使其熱強性大大降低,加工塑性變壞,如果鎳基合金采用真空冶煉后Pb的含量由5x10-6降至2x10-6以下,其持久強度可增加一倍。因此,通過改善冶金工藝提高蠕變和持久強度的途徑如下:
表面細晶粒、中心粗晶提高疲勞性能,即在鑄造模套內部加細化晶粒的成核劑。
定向凝固。高溫合金在長期工作的情況下,裂紋一般沿垂直于應力方向的橫向晶界產生并沿晶斷裂。定向結晶工藝就使柱狀晶沿受力方向生長,消除橫向晶界,從而大大提高 持久壽命。
3、試驗因素的影響
1)試驗溫度
溫度對蠕變和持久強度有很大影響。蠕變本身是一個熱激活的過程,可用狀態(tài)方程表示為
式中ε-蠕變速率;A-常數;Q-蠕變激活能;R-氣體常數;T-指定溫度(K)。
2)試驗加載同心度的影響
實際上是應力的影響問題,若加載作用線和試樣軸線不重合,則試樣除受到拉應力外,還附加了彎曲應力。按試樣承受的負荷及截面計算的應力往往小于試樣表面的最大應力。Pemney和Ellison通過研究偏心率對蠕變的影響,了解到為保證蠕變數據具有較好的重復性,彎曲度應控制在5%以內。
參考文獻:郭廣平, 丁傳富.航空材料力學性能檢測 〔M].北京:機械工業(yè) 出版社,2017.
免責聲明:本網站所轉載的文字、圖片與視頻資料版權歸原創(chuàng)作者所有,如果涉及侵權,請第一時間聯系本網刪除。
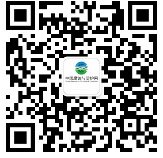
官方微信
《腐蝕與防護網電子期刊》征訂啟事
- 投稿聯系:編輯部
- 電話:010-62316606
- 郵箱:fsfhzy666@163.com
- 腐蝕與防護網官方QQ群:140808414