多孔金屬膜產生于20 世紀40 年代,為分離鈾同位素而發明了金屬Ni 膜,但其熱穩定性較差。在隨后幾十年里,以Al2O3陶瓷為基體的陶瓷膜發展迅速,但由于陶瓷膜難以適應溫度的變化,在使用過程中易發生斷裂,無法長時間在腐蝕液體、水蒸氣和高壓力等環境中工作,使用性能受到限制。將多孔金屬與陶瓷復合,可以發揮其各自優點。20世紀90 年代,美國成功研制出以多孔不銹鋼為基體,TiO2陶瓷為膜層的“Scepter”膜,其具有滲透量大、過濾精度高和力學性能好等優點,迅速被應用于石油化工、生物制藥、食品、紡織工業和制漿造紙等領域。
目前生產多孔金屬陶瓷膜的企業主要有德國GKN 公司(Scepter),新加坡Hyflux 公司(Ferro-Cep),美國Graver(Scepter)、Pall (AccuSep)、Osmonics(Duratrex)、Dupont 和Mott 公司,英國FaireyMicrofiltrex公司,韓國Fiber Tech 公司和日本HitachiMetals 公司等,生產的陶瓷膜孔徑大多在0.02~0.10 μm之間。南京工業大學膜科所、西北有色金屬研究院和鋼鐵研究總院在無機膜的研究方面處于國內領先,安泰科技作為國內個別掌握金屬微孔膜核心生產技術的單位之一,其已商業化的多孔金屬膜孔徑最小為0.05~0.10 μm。由于多孔金屬陶瓷膜在國內尚屬起步階段,而GKN 和Hyflux 兩家公司已基本完成多孔金屬陶瓷膜在中國的布局,進一步拉大了國內與國外的研究距離。本文通過介紹國內外不同多孔金屬陶瓷膜的結構特點、制備工藝和技術參數等,為多孔金屬陶瓷膜的制備提供先進的研究范例和理論參考。
1 多孔金屬陶瓷膜的結構特點
多孔金屬陶瓷膜通常由3 部分構成:一是具有高孔隙率、大孔徑的金屬基體,作為支撐膜層;二是具有選擇性的過濾膜層(TiO2、Al2O3、SiO2和ZrO2膜等),使大的顆粒物難以進入濾膜內部;三是處于基體和膜層之間的過渡層,其作用是實現孔徑的過渡,防止膜層顆粒大量進入基體,降低滲透量,同時可使兩層更好地結合,保證膜層的完整性。
由于膜層制備工藝是金屬陶瓷膜制備技術中的核心機密,國外研究鮮有提及。圖1 為Hyflux 公司生產的FerroCep 膜的交叉網格結構。其特有的涂層制作工藝,使得TiO2涂層與多孔316L 不銹鋼支撐體牢固結合,形成了堅固的交叉網絡結構多孔金屬陶瓷膜,圖中TiO2 膜孔徑為0.1 μm,厚度為10.0 μm,TiO2粉體滲入基體大約10.0 μm,既保證了結合強度,又不影響金屬基體的滲透率。圖2為一般情況下多孔金屬、多孔金屬金屬膜、多孔金屬陶瓷膜和多孔陶瓷的水滲透量和壓降的關系。可以看出,多孔膜結構兼顧了流量與能耗,這也是多孔金屬陶瓷膜能夠迅速發展的主要原因。
2 多孔金屬陶瓷膜的制備方法
適合于制備多孔金屬陶瓷膜的方法主要包括懸浮粒子燒結法、絲網印刷法、溶膠凝膠法、陽極氧化法和電泳沉積法等。目前批量生產陶瓷膜一般采用濕粉噴涂法(圖3(a))和絲網印刷法(圖3(b)),而溶膠凝膠法和電泳沉積法是實驗室常用的制備陶瓷膜方法。濕粉噴涂法是GKN公司專利,在多孔金屬陶瓷膜的生產和研究中應用較多。由于每種制備方法具有各自的優缺點,有時也將2 種方法結合來制備膜層。
懸浮粒子燒結法是將金屬或陶瓷粉末顆粒與造孔劑、粘結劑和分散劑等原料球磨制備成穩定的懸浮液——粉漿或膠體,然后采用常規浸涂法、刷涂法、濕粉噴涂法、熱噴涂法和離心沉積法等制備膜層。絲網印刷法是通過滾軸的壓力使膏糊狀的陶瓷粉末經過絲網在多孔金屬基體表面成形的方法。由于陶瓷制膜液難以對金屬支撐體形成良好的潤濕,該方法制備的膜層牢固性較差;對于孔徑較大的金屬基體,燒結時收縮力大,膜層易開裂;同時由于粉末越細,表面能越大,容易團聚,因此懸浮液需要注意控制粉末的分散、膜層干燥速率和懸浮液黏度等。由于常規浸涂法和刷涂法僅靠毛細管力作用,無法改善金屬與陶瓷界面的結合,而濕粉噴涂法、熱噴涂和絲網印刷法多采用壓力成形,有利于增強界面結合力。
溶膠凝膠法是制備多孔陶瓷膜的傳統方法之一。涂膜方式主要有旋涂法、提拉成膜法和噴涂法等。采用溶膠-凝膠技術制備無機膜工藝簡單,合成溫度低,得到的產品純度高、化學組分均勻,制得的膜孔徑小且孔徑分布范圍窄。由于制備過程中需要大量的有機溶劑,成本較高。同時薄膜與基體的附著力較差,對溶膠的配制和多孔金屬基體的要求很高,涂膜干燥燒結易出現龜裂現象。
陽極氧化法是將多孔膜層在室溫下酸性介質中進行陽極氧化,再用強酸提取,除去未被氧化的部分,制得微孔金屬氧化膜。電泳沉積法(圖3(c))是由膠體粒子在分散介質中向電極遷移后沉積在電極表面,并通過顆粒團聚形成均質多孔膜。陽極氧化法主要用來制備Al2O3陶瓷膜,電泳沉積法則適合制備幾乎所有的陶瓷膜。此外還有一些方法如磁控濺射法和化學氣相沉積法等也都用來嘗試制備多孔金屬陶瓷膜。
3 多孔金屬基體
Biesheuvel 等認為要成功制備出多孔金屬陶瓷膜材料,基體材料需要保證高強度、一定的滲透率和光滑的表面。因此一般選擇的金屬支撐體為多孔不銹鋼、多孔Ti、多孔Ni 和多孔金屬間化合物等。這類金屬基體采用粉末或纖維燒結得到,具有耐高溫、耐腐蝕、可焊接等優點,是制備膜材料良好的基體。
基體孔徑大小、孔隙形狀和金屬基體粉末形態等影響著成膜時的毛細管力,進而影響最終膜的完整性和膜孔大小分布。李忠宏發現在1.0 μm的多孔基體上可以較容易地制備連續的具有顆粒形貌、孔徑均勻的多孔陶瓷膜;而當基體孔徑達到1.5 μm時,膜層的連續性就會受到影響,但并不嚴重,可以用制備過渡層的方法制備連續的多孔膜層;當基體孔徑達到3.0 μm以上時,膜層就無法連續。圖4 分別為孔徑為5.0 μm和1.0 μm的多孔不銹鋼表面的TiO2膜形貌。LI 等認為不均勻的表面和球形的多孔金屬基體孔隙會造成膜層表面產生裂紋。ZHAN等發現由于多孔Ti 顆粒和孔隙呈不規則多邊形,采用溶膠凝膠法多次提拉后燒結的膜表面出現較多圓形狀剝落,圖4(c)為孔徑1.1 μm的多孔Ti 采用溶膠凝膠法3次提拉后的燒結膜層。
基體的表面質量對膜層的潤濕性有很大影響,決定著金屬基體與膜的結合強度。Biesheuvel 等認為支撐體需要光滑的表面,這樣才能制備出沒有缺陷的薄膜,Meulenberg 等在表面粗糙度Ra=(0.256±0.008)μm 的多孔316L 表面制備出完整TiO2膜,但是李忠宏和奚正平認為在一定的要求范圍內,支撐體的孔徑越大,表面質量越差,這些凹凸不平的部位可以提供膜層中顆粒形成的“核心”,因此膜層顆粒形成就越充分,結合強度越高。
4 多孔陶瓷膜
4.1 TiO2多孔膜
TiO2膜的燒結溫度比Al2O3、ZrO2膜低,同時具有比較窄的孔徑分布,是商業運用比較早的多孔金屬陶瓷膜,在污水處理、空氣凈化、醫用抗菌防腐、光催化劑等方面有著誘人的應用發展前景。但TiO2是一種缺氧化合物,溫度和氧分壓對其晶體結構、化學成分和性能有很大影響。Gill 等采用懸浮粒子燒結法在多孔Ni 基合金上制備出過濾精度為0.1 μm的氧化鈦膜,還原氣氛燒結使得最初的金紅石相的TiO2 多數轉變為Ti4O7、Ti2O3 和Ti6O11。LI 等和Meulenberg 等[18]利用絲網印刷法和濕粉噴涂法在多孔不銹鋼基體上制備出孔徑為0.11 μm的TiO2膜,發現絲網印刷法制備的膜層具有高的燒結密度和表面質量,而濕粉噴涂法制備的膜層具有較高的結合強度。同時發現真空950 ℃燒結1 h 的TiO2膜為深藍色,但在空氣中600 ℃燒結1 h 后又變為白色,其給出一種解釋可能是Ti4+發生了還原,例如出現如Ti4O7的亞穩相,但XRD試驗中發現金紅石TiO2 相仍然占有很大比例,出現了Cr0.12Ti0.78O1.74相,并未檢測到Ti4O7亞穩相,最后強調了以多孔金屬為基體的TiO2膜不能長時間在氧化氣氛下熱處理。魏磊等提出了一種碳輔助的固態粒子燒結法,利用PVA在N2中高溫碳化生成碳,所形成的TiO2和碳的混合結構削弱了因載體表面狀況差和陶瓷金屬間熱膨脹系數不匹配而引起的陶瓷層燒結應力,成功制得膜層厚度約為10.0 μm,平均孔徑為0.21 μm的不銹鋼/TiO2膜。周守勇等研究了空氣和Ar燒結氣氛對對稱TiO2膜微觀組織的影響,發現TiO2膜在空氣中的燒結活性要比在Ar中高,在低的O2分壓下燒結會出現Ti3+,并出現TixOy 新相,其中y<2x。
國內對多孔金屬陶瓷的研究多采用溶膠凝膠法。實驗發現溶膠性能主要影響膜層形貌和成膜的結合強度,而燒結溫度決定著最終成形的孔徑和TiO2相結構,當燒結溫度過高或在燒結過程中通入O2,可得到幾乎沒有孔隙的膜層。但為了防止多孔金屬基體被氧化,TiO2膜一般在還原氣體、惰性氣體或真空環境中燒結。范益群等采用改進浸漿法在多孔Ti 基體上制備了氧化鈦微濾膜,將氧化鈦粉體分散到氧化鈦溶膠中作為制膜液,以提高制膜液在多孔金屬支撐體表面的潤濕性。結果表明,相同溫度下溶膠的表面張力遠小于水的表面張力,溶膠分散制膜液的表面張力也遠小于水分散制膜液的表面張力。由此顯著地改變了制膜液和支撐體的潤濕性能,可以在850 ℃下燒結得到平均孔徑為0.31 μm的連續完整膜層。
采用懸浮粒子法和溶膠凝膠法制備膜層都需要注意控制干燥速率和懸浮液黏度。干燥速率較快時,膜層表面易出現裂紋,圖5(a)為濕粉噴涂法在較快干燥速率下產生的裂紋,圖5(b)為采用溶膠凝膠法時不穩定的溶膠燒結產生的龜裂現象。懸浮液或溶膠黏度較大時,膜層與基體結合界面明顯,無法滲入基體增強結合力。保持合適的黏度,膜層既可形成網狀結構,增強與基體的結合力,也可以避免膜層粒子大量進入基體造成滲透率的降低。圖6(a)、(b)分別為低、高黏度下膜層粒子與基體結合的SEM照片。
電泳沉積法和陽極氧化法制備的膜層表面均勻性差,因此一般結合溶膠凝膠法或懸浮粒子法來制備。周守勇等采用電泳沉積結合浸涂的方法制備多孔Ti-Al合金基TiO2膜,通過在Ar中1 050 ℃燒結3 h得到的TiO2/Ti-Al 復合膜,平均孔徑為0.28 μm,厚度為40 μm左右,純水通量4.69×10-4 mol/(m2·s·pa)。湯慧萍等在多孔不銹鋼基體上燒結多孔金屬膜層,然后將多孔膜層浸入電解液中陽極氧化5~30 min,獲得氧化物納米多孔結構過渡層,最后在過渡層表面涂覆氧化物粉末(TiO2等)后燒結,獲得孔徑為50 nm,厚度為2.0 μm的陶瓷膜。
4.2 Al2O3多孔膜
多孔Al2O3陶瓷膜是膜材料中研究較早也是最廣泛的一種,具有化學穩定性好、電阻率高、耐高溫、耐腐蝕、滲透率高等優點。但由于Al2O3膜燒結溫度較高,因此多采用溶膠凝膠法來制備。通常Al2O3膜是作為致密Pd 膜或其他陶瓷膜的襯底,用以增強實際作用膜的選擇性和滲透量。
提高Al2O3陶瓷膜與多孔金屬基體的結合強度和表面質量是研究Al2O3陶瓷膜的重點。一方面可以通過在膜層中引入一些金屬元素(Ag、Ni、Cu 和Fe 等)來增強陶瓷膜和多孔金屬基體的浸潤性,如魏磊等采用懸浮粒子燒結法制備了平均孔徑為0.2~3.9 μm,膜厚為40~50 μm 的Al2O3/不銹鋼微濾膜,發現在基體與Al2O3膜層間預先引入一層不銹鋼細粉作為過渡層再進行共燒,可以有效地解決Al2O3膜層易于剝落的問題。而趙靜靜等采用溶膠凝膠法發現在多孔不銹鋼基體和Al2O3底膜間引入Cu合金連接的結合力比未引入連接層的Al2O3膜結合力提高了317%。另一方面配制穩定、均勻的溶膠是制備出高質量無缺陷的Al2O3陶瓷膜的關鍵,李東風等以勃姆石粉體為原料,采用溶膠凝膠法在孔徑為8.0~13.0 μm的多孔不銹鋼基體上附載一層Al2O3 膜,在Al2O3 濃度5.0%(質量分數),酸量0.07,添加劑40.0%(質量分數)的條件下制備的溶膠粒度小、黏度低,制得的Al2O3膜質量較好。
燒結溫度對Al2O3陶瓷膜孔徑和Al2O3的晶體結構有很大影響。LIN 等發現γ-Al2O3膜的孔徑在超過1 000 ℃左右時迅速增大,但向溶膠中加入3.0%(質量分數)的La獲得的孔徑為25 nm的陶瓷膜能夠在1 200 ℃加熱30 h 保持穩定,而未加La 的γ-Al2O3全部轉化為α-Al2O3,說明加La能夠提高Al2O3膜的相變點大約200 ℃。李忠宏等[40]采用溶膠凝膠法在316L 多孔不銹鋼上制備Al2O3過渡層以支撐TiO2、SiO2和TiO2-SiO2的復合膜,當燒結溫度為1 000 ℃時可獲得晶粒尺寸為3.0 μm的γ-Al2O3膜,當燒結溫度達到1 200 ℃時,γ-Al2O3全部轉化為晶粒尺寸為5.0 μm的α-Al2O3,最后可獲得厚度為5.0 μm、孔徑為0.7 μm的α-Al2O3膜。
Al2O3膜作為過渡層時可以很好地連接基體和表面作用膜,最大限度地發揮表面膜的作用。胡海等采用溶膠凝膠法以泡沫Ni 為基體,A12O3作為過渡中間層,制成泡沫金屬基的TiO2和TiO2/A12O3膜層,由于A12O3過渡層增大了載體的比表面積,具有吸附濃縮作用,同時也增加了負載光催化劑的活性位數量,從而具有更高的催化活性。Chi 等在制備Pd膜之前采用兩步法對多孔不銹鋼進行修飾,通過加壓噴涂的方法,用超聲分散的大顆粒Al2O3溶液對基體進行第1 次涂膜,同樣的方法將分散好的小顆粒Al2O3溶液對基體進行第2 次涂膜,通過梯度涂膜縮小基體的孔徑,取得了較好的表面修飾效果。
4.3 SiO2多孔膜
SiO2膜可以提高金屬表面硬度,增強其耐磨性,同時也經常被用來制備分子篩等分離材料。黃子安等采用溶膠凝膠法以孔徑為20~40 μm的多孔金屬Ti 片為載體,通過反復多次浸涂、干燥和煅燒工藝制備了擔載型多孔Ti 基SiO2復合膜,孔徑分布范圍為4.0~8.0 nm,所制備的膜沒有明顯的裂紋和溝道,但表面均勻性差,對多孔Ti 片涂膜的前處理工藝有待改進。田茂東和張守臣等采用溶膠凝膠法控制Si 凝膠顆粒的粒度,經6 次涂敷、陳化和燒結后,成功在多孔金屬Ti表面制備出SiO2膜,可用于分離聚乙二醇和玉米蛋白水溶液。Castro 等采用溶膠凝膠法在pH 值為6 時制備出厚度為4.5 μm的SiO2膜層,之后又結合電沉積法在500 ℃燒結0.5 h后制備出厚度為12.0 μm的膜層且具有良好的耐腐蝕性。
韓國Lee 等在多孔不銹鋼基體上用溶膠凝膠法制備了SiO2膜層來分離H2和N2。該陶瓷膜層由3層組成,第1 層是利用膠溶法在多孔不銹鋼基體上制備了大顆粒的SiO2膜以修飾不銹鋼的表面缺陷,然后在大顆粒的SiO2膜上制備Al2O3膜作為過渡層(第2 層),最后用聚合法制備了小顆粒的SiO2頂膜(第3 層)。該膜層的形貌欠佳,同時膜層的熱穩定性也不好,當工作溫度超過250 ℃時,膜對H2和N2的分離功能就會喪失。為了進一步提高膜層性能,其團隊利用旋轉蒸發儀獲得了粒子尺寸500 nm 和100 nm的干燥SiO2凝膠,在10 MPa 壓力下將干燥凝膠壓縮到大孔隙不銹鋼上,然后在600 ℃下煅燒,達到界面修飾的目的,最后采用浸潤軋制的方法制得底膜,獲得了熱穩定性較好無缺陷的分離膜。浸潤軋制可以直接在孔隙處制備膜層,這樣膜層在使用時可以減少損傷,最大限度發揮膜層功效,同時也可以用來修復底膜缺陷。圖7(a)、(b)和(c)分別為浸潤提拉膜層示意圖、浸潤軋制膜層示意圖和膜層SEM照片。
4.4 ZrO2多孔膜
ZrO2膜相比TiO2、Al2O3和SiO2膜具有更好的力學強度、化學耐久性和抗堿浸蝕等特性,在高溫陶瓷膜領域得到了廣泛的研究。在Nice 世界過濾大會上Alcan Separations 公司公布了一種由Ni 基超級合金網支撐,表面涂以ZrO2的金屬陶瓷膜,孔徑大小0.2 μm,過濾純水的流量為1.54×10-4mol/(m2·s·Pa),可在60 ℃、1.0%(質量分數)NaOH或HNO3中使用,耐130 ℃蒸氣消毒和反沖洗。Herrmann 等制備出一種以多孔316L不銹鋼絲網為基體的陶瓷膜,通過多層梯度化的絲網支撐體獲得了平均孔徑為0.005~10.000 μm的膜層,膜層材料包括ZrO2、TiO2和Y2O3等。圖8 為以多孔不銹鋼絲網為基體的膜層SEM照片。可以看出,由于絲網的特殊結構,膜層與基體的結合強度不高。Tarditi 等在0.1~0.2 μm的多孔不銹鋼基體上制備Pd-Cu 膜時,為了避免金屬擴散和減小金屬膜的厚度,采用真空浸涂的方法制備了ZrO2中間膜層。發現采用2 個沉積周期,中間500 ℃煅燒5 h,制備出的ZrO2膜與基體的結合強度和孔隙處ZrO2顆粒的數量都要比沒有進行中間煅燒的好。
5 發展趨勢
膜層孔徑的納米化:以多孔不銹鋼為基體的膜層材料最重要的作用就是過濾和分離。隨著工業的發展,過濾行業對過濾精度的要求越來越高,過濾孔徑逐步向超微米級、納米級發展,如Hyflux 研制的不銹鋼TiO2微濾膜孔徑可達20 nm,已成功應用在制藥、食品等領域,因此陶瓷膜納米化是未來研究方向之一,可促使多孔金屬陶瓷膜由過濾向氣體分離領域拓展。
基體與膜層結構的梯度化:楊保軍等采用離心沉積法制備了梯度多孔Ni,梯度層的最佳匹配厚度與所沉積的粉末平均粒度呈線性關系。梯度化設計增強了多孔材料各層之間的結合強度和對壓力的適應性,使多孔材料具有了高精度和大透過量,解決了孔徑與相對透氣系數之間的矛盾,可以更好地適應環境的變化。
基體與膜層材質的復合化:隨著應用領域的不斷拓展,金屬多孔基體向著合金化發展,如耐高溫、耐腐蝕、抗氧化的FeCrAl、FeAl、NiCr 等金屬間化合物,以及新型不銹鋼和Ni 基合金的研究最為廣泛。為了充分發揮膜的功效,研究者采用復合膜結構膜摻雜的方法制備出了TiO2-ZrO2、SiO2-A12O3、TiO2-A12O3等多孔復合膜分離催化材料,多層復合膜是未來多孔金屬陶瓷膜發展的重點。
6 結束語
雖然多孔金屬陶瓷膜存在著諸如金屬與陶瓷結合力不高、膜層不均勻、價格偏高等問題,但從多孔不銹鋼TiO2膜的快速發展可以看出多孔金屬陶瓷膜具有廣闊的工業應用和發展前景,這些問題也會隨著實踐和研究的發展而得到解決。隨著國內對環境污染、制造粗放和能源浪費等問題的重視,勢必會加快多孔金屬陶瓷膜相關的理論基礎和工藝的研究,打破國外金屬陶瓷膜的壟斷,推動膜工業的發展。
更多關于材料方面、材料腐蝕控制、材料科普等等方面的國內外最新動態,我們網站會不斷更新。希望大家一直關注中國腐蝕與防護網http://www.ecorr.org
責任編輯:王元
《中國腐蝕與防護網電子期刊》征訂啟事
投稿聯系:編輯部
電話:010-62313558-806
郵箱:ecorr_org@163.com
中國腐蝕與防護網官方 QQ群:140808414
免責聲明:本網站所轉載的文字、圖片與視頻資料版權歸原創作者所有,如果涉及侵權,請第一時間聯系本網刪除。
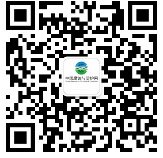
官方微信
《腐蝕與防護網電子期刊》征訂啟事
- 投稿聯系:編輯部
- 電話:010-62316606-806
- 郵箱:fsfhzy666@163.com
- 腐蝕與防護網官方QQ群:140808414