1 高性能混凝土國內(nèi)外現(xiàn)狀與展望
1.1 高性能混凝土的涵義
高性能混凝土一詞是從英文 High Performance Concrete (HPC) 翻譯過來的,是近年來一些發(fā)達國家基于混凝土結構耐久性設計提出的新概念的混凝土。區(qū)別于傳統(tǒng)混凝土,高性能混凝土把混凝土結構的耐久性作為首要的技術批標,目的在于通過對混凝土材料硬化前后各種性能的改善,提高混凝土結構的耐久性和可靠性。
1.2 國外高性能混凝土的發(fā)展情況與國內(nèi)高性能混凝土的現(xiàn)狀
由于高性能的混凝土密實性能好,變形小,抗?jié)B、抗凍性能和耐侵蝕能力均優(yōu)于普通混凝土,使用壽命長。因此,建造經(jīng)久耐用的工程必須用高性能混凝土。國外已有很多應用實例,如20世紀90 年代,美國、加拿大、日本、挪威、前蘇聯(lián)各國、德國、澳大利亞等,成為應用最多的國家。近幾年我國也開始研究和應用高性能混凝土,最早是上海南浦大橋配制C40混凝土泵送高達154m的工程,以及杭州灣大橋和現(xiàn)正在建的鐵路客運專線鐵路工程施工的混凝土都按100年使用年限設計的高性能混凝土。
第二章 高性能混凝土的配制
配制高性能混凝土,從原材料上,除了常規(guī)的水泥、砂、石和水這四種材料外,必需使用化學外加劑和礦物細摻料,一共是六種必不可少的材料,而且后兩種可以是一種也可以是多種復合,這在選材上就要求與水泥具有良好的相容性,多種的外加劑之間(或細摻料之間)要求合理匹配,使具有黃金搭配,疊加效應的效果,增加了選材的復雜性;從配比上,為了適應高耐久、高強的要求,使用的是低用水量(<180kg/m,低水膠比(一般為0.28~0.40),控制膠凝材料總量≯550kg/m;從性能上,具有高耐久性(抗?jié)B、抗凍、抗蝕、抗碳化、抗堿骨料反應,耐磨等);良好的施工性(大流動,可灌性、可泵性、均勻性等);良好的力學性能,早期強度合適,后期強度高;良好的尺寸穩(wěn)定性;合理的適用性與經(jīng)濟性等。總之,具有良好的綜合技術性能,能滿足各種工程結構的使用要求,使用壽命至少100年以上。
2.1 高性能混凝土原材料選擇及品質(zhì)鑒定
2.1.1水泥
水泥和混凝土的關系,前者是后者產(chǎn)品質(zhì)量的賴以生存的根基。水泥細度、礦物組成、以及堿含量都是影響混凝土質(zhì)量主要原因。
水泥中含堿量:水泥中含堿量過大,容易與活性骨料產(chǎn)生二次反應,體積膨脹促使混凝土開裂,即堿-骨料反應。即是沒有活性骨料,過多的堿也是促進水泥的收縮開裂,造成混凝土結構物的劣化。
2.1.2高效減水劑
高效減水劑(或緩凝劑高效減水劑)是現(xiàn)代高性能混凝土必要的組分。高效減水劑使得混凝土的水膠比降大大降低卻仍有很好的工作性。它的作用機理是能打破水的表面張力,將物料顆粒包圍的游離水釋放出來,發(fā)揮吸附和潤滑作用,使在保持混凝土坍落度不變情況下,單位用水量減少。且能與水泥中的游離氧化物產(chǎn)生凝膠作用,阻塞混凝土中的空隙,使外界水不能滲進混凝土內(nèi),因此摻減水劑的混凝土抗?jié)B指標可比普通混凝土提高2~3倍。由于減水劑與硅灰、粉煤灰、磨細礦渣粉等摻合料在混凝土中各自產(chǎn)生的作用機理不同,二者互不干擾,作用迭加。
2.1.3礦物活性摻合料
礦物活性摻合料也稱混凝土外摻料,主要品種有粉煤灰、硅灰、和磨細礦渣等。另外還有天然沸石粉、磨細石灰石粉、石英砂粉也可以作為混凝土的外摻料。后3種很少使用。
2.1.4骨料
品質(zhì)符合要求的硅質(zhì)河砂。石灰?guī)r碎石,兩種粒級二級配:5~10㎜占30%、10~25㎜占70%,混合后符合要求。
2.1.5 混凝土拌合用水:使用飲用水
2.2 高性能混凝土配合比設計
高性能混凝土的配合比設計與普通混凝土不同,首先要保證耐久性要求,考慮到抗碳化性、抗化學侵蝕性、抗凍性、抗堿骨料反應、抗干燥收縮的體積穩(wěn)定性、抗大氣作用性、耐磨性。做試配時需要檢驗項目:坍落度、泌水率、含氣量、抗裂性、抗壓強度、彈性模量、電通量、抗凍性、耐磨性、抗?jié)B性等。
2.2.1配合比設計的基本原理
混凝土配合比設計的目標,是要確定能滿足工程技術要求的各種材料用量,配合比設計原理要依據(jù)三大法則。
1)水灰比(或灰水比)法則
水灰比的大小決定混凝土硬化后的強度,并影響硬化混凝土的耐久性。
混凝土的強度與水泥強度成正比,與水灰比成反比,這個規(guī)律仍然不變。具體可用強度公式表示如,根據(jù)這一法則確定水灰比,以保證混凝土的強度和耐久性,對高性能混凝土,由于將礦物細摻料當作膠結材的一部分因此計算的應該是水膠比(或膠水比),且礦物細摻料品種與摻量的不同對公式中系數(shù)和值會有所變化。對于高性能混凝土,按現(xiàn)代高性能混凝土技術配制,以低水膠比(一般都不大于0.40,對所處環(huán)境不惡劣的工程可以放寬)、低用水量,混凝土密實度高為前提,以耐久性作為主要控制指標,保證配制的混凝土達到百年使用壽命。滿足用戶要求的和易性,適應工程條件施工。
2)最大密實度法則
該法則的基本思路是各項材料互相填充空隙,以達到混凝土密實度最大,換言之就是各項材料的密實體積總和等于1m絕對密實的混凝土,即:
砂率的確定,高性能混凝土的砂率一般取決于骨料的級配和顆粒形狀、水泥漿的流變性(體現(xiàn)在水膠比和單位用水量這兩個參數(shù)上)和混凝土的工作性(坍落度)。由于高性能混凝土中的水泥漿體積相對較大,故通常砂率偏高,根據(jù)和易性要求,砂率應在骨料總體積的34%~40%范圍內(nèi)取值(水下灌注混凝土按40%~45%范圍內(nèi)取值),從中確定配合比中的漿集比與砂率,以確保混凝土的強度、耐久性與經(jīng)濟性。
3)最小單位用水量法則
在和易性允許的條件下,混凝土的單位用水量應盡可能小。對于高性能混凝土來說,主要考慮坍落度與使用的高效減水劑的減水效果及礦物摻合料的關系。
2.2.2配合比設計思路
按絕對體積法
膠凝材料漿體 = 水泥 + 水 + 外加劑 + 摻合料
骨料體積 = 砂 + 石子
需要確定的參數(shù)為:試配強度、水膠比、用水量、漿集比、砂率、外加劑摻量、摻合料摻量等7項。
具體可分三大步驟:
(1)先計算空白混凝土的初步配合比,
(2) 根據(jù)經(jīng)驗初步確定外加劑與細摻料的摻量,通過流動性的試驗調(diào)整,和抗裂性的對比試驗確定基準配合比,
(3)再經(jīng)過強度與耐久性試驗調(diào)整,確定試驗室理論配合比,最后通過含水率的換算確定施工配合比。
2.2.3配制的三大技術關鍵
在配合比設計過程中兩次試驗調(diào)整是很重要的兩個階段,要解決好兩次試驗調(diào)整,必需掌握三大技術關鍵。
1)合理使用各種外加劑的技術,包括外加劑的選用,各種外加劑間的復合,外加劑的最佳摻量,如何達到與水泥間的相容性良好,混凝土坍落度經(jīng)時損失小的要求。
2)合理使用摻合料的技術,包括摻合料的選用,各種摻合料間的復合,摻合料的摻量,可選確定不同的方案,通過流動性,抗裂性,強度與耐久性對比試驗,進行優(yōu)選。
3)卓有成效地控制混凝土開裂和防裂的技術,包括原材料選用,水化熱控制,配合比參數(shù)(水膠比,用水量)的控制,施工中溫度的控制,養(yǎng)護措施的保證等。
2.3 配制高性能混凝土時粉煤灰摻入量選擇
2.3.1為了提高混凝土的耐久性,改善混凝土的施工性能和抗裂性能,混凝土中應適量摻加優(yōu)質(zhì)粉煤灰、磨細礦渣粉或硅灰等礦物摻合料。不同礦物摻合料的摻量應根據(jù)混凝土的性能通過試驗確定。一般情況下,礦物摻合料的摻量不宜小于膠凝材料總量的20%。當混凝土中粉煤灰摻量大于30%時,混凝土的水膠比不宜大于0.45。預應力混凝土以及處于凍融環(huán)境中的混凝土的粉煤灰的摻量不宜大于30%。
2.3.2 C30及以下混凝土的膠凝材料總量不宜高于400㎏/m,C35~C40混凝土不宜高于㎏/m,C50及以上混凝土不宜高于500㎏/m。
2.3.3不同環(huán)境條件下鋼筋混凝土及預應力混凝土結構的混凝土的水膠比、膠凝材料用量應足規(guī)范的規(guī)定。
2.3.4當化學侵蝕介質(zhì)為硫酸鹽時,除了配合比參數(shù)應滿足規(guī)范的規(guī)定外,且膠凝材料的抗蝕系數(shù)K應小于0.80。
2.4 高性能混凝土配合比設計步驟
2.4.1試配強度的確定
高性能混凝土試配強度必須超過設計要求的強度標準值以滿足強度保證率的需要,其超出的數(shù)值應根據(jù)混凝土強度標準差而定。
混凝土配制強度按下式計算:
2.4.5初步砂率:根據(jù)混凝土不同使用部位,泵送混凝土灌筑按34%~38%,水下灌注混凝土按40%~45%選用。
3.4.6膠漿量:
即水泥與摻合料加水和含氣量的體積。
2.5 高性能混凝土配合比試驗結果
2.5.1京津城際C50級高性能混凝土試驗配合比、材料用量及混凝土物理性能試驗結果
C50級混凝土試驗配合比材料用量表
表1
第三章 高性能混凝土施工
高性能混凝土要求密實性能好,變形小,抗?jié)B、抗凍性能和耐侵蝕能力均優(yōu)于普通混凝土。混凝土施工要對整個工藝進行全面控制,包括模板的選用與支立、各種原材料品質(zhì)、配制量、拌合、灌筑、搗固、養(yǎng)生等聚工藝要有個控制范圍,使?jié)仓幕炷脸叽鐪蚀_、棱角分明、表面平整光滑、顏色一致、強度符合設計要求、內(nèi)部密實不滲水。
3.1 模板
3.1.1 選用表面平整、光潔度好的鋼制模板或有加固系統(tǒng)的涂膠板。模板支承系統(tǒng),在計算荷載作用下,按受力程序分別進行驗算,確保其強度、整體剛度和穩(wěn)定性,安裝時接縫要嚴密不漏漿。對于塑性混凝土,模板支承力與混凝土灌筑方法及混凝土的初凝時間有關,見下式所示:
3.1.2模板隔離劑,可選用商品成品隔離劑,也可用工業(yè)油類在現(xiàn)場自配。商品成品混凝土模板隔離劑品種繁多,最常用的有乳化機油類隔離劑和甲基硅樹酯類隔離劑。乳化機油模板隔離劑產(chǎn)品很稠,使用時用水沖淡,用于鋼模時1份乳化劑加5份清水,攪均后噴涂。該產(chǎn)品脫模容易,便于涂刷,制品表面光滑,使用時注意鋼筋不要粘油。甲基硅樹酯模板隔離劑是用甲基硅樹酯加固化劑和適量的稀釋劑配制而成,該產(chǎn)品涂于模板表面堅硬光滑,涂一層可重復使用4~6次,但產(chǎn)品價格較高,適用于不受碰撞的襯砌臺車,小模板由于多是人工拆模,易碰壞板面,故一般不采用。在現(xiàn)場自配混凝土模板隔離劑,可用機油1份加柴油3份混合攪拌均勻后,用布蘸本劑擦于模板即可,效果同于乳化機油模板隔離劑。模板涂抹隔離劑前,應將模板面的圬物清除干凈再涂刷隔離劑。
3.2 混凝土施工配料拌合
3.2.1配料:配料時計量設備在使用前應進行校核,按配合比配料的允許誤差(以質(zhì)量計)不超過規(guī)范的規(guī)定。
3.2.2拌合:混凝土拌合應均勻,每盤最短拌合時間應符合規(guī)范要求。
3.3 混凝土的灌筑與搗固
3.3.1混凝土灌筑
(1)攪拌站距離灌筑地點盡量近一些,避免長距離運輸混凝土坍落度損失大。如用輸送泵灌筑混凝土,一臺輸送泵應配兩臺以上輸送車,保證混凝土連續(xù)泵送。
(2)混凝土灌筑布料應均勻,按每灌筑30cm厚度搗固一次,灌筑時應有專用的布料工具整平混凝土后再振搗。
3.3.2混凝土搗固
混凝土振搗采用模內(nèi)插入式振搗器,振搗器距模板20cm左右,垂直快速插入混凝土內(nèi),每在一個位置上的振動時間,應保證混凝土獲得足夠的密實度,并要注意不要振動過度,防止混凝土表面出現(xiàn)砂面。振搗器拔出混凝土時速度要慢,保證振動棒周圍的空氣能夠跟隨振動棒引出。
每層混凝土振搗過后要用搗固鏟沿模板插邊,將模邊滯留的氣泡排出。
3.3.3混凝土養(yǎng)護
1)混凝土澆筑完畢并初凝后,應盡快加以復蓋保濕,保持混凝土表面濕潤,混凝土保濕養(yǎng)護日期不少于21天。
2)混凝土養(yǎng)護也可在澆筑完畢并初凝后噴灑或涂刷養(yǎng)護劑進行養(yǎng)護。或包裹塑料布(其內(nèi)事先澆淡水使之形成蒸氣)密閉養(yǎng)護。
3.3.4混凝土拆模
混凝土灌筑后的拆模時間,由技術人員根據(jù)混凝土達到拆模強度掌握,按《混凝土及鋼筋混凝土施工驗收規(guī)范》執(zhí)行。
3.4 混凝土質(zhì)量控制和檢查(按規(guī)范要求進行)
第四章 混凝土施工可能出現(xiàn)問題的現(xiàn)象、原因及注意避免
4.1 混凝土拌合物泌水
4.1.1新拌混凝土發(fā)生泌水的原因:
混凝土由水、膠凝材料、細骨料、粗骨料、外加劑等拌合而成,質(zhì)量好的新拌混凝土應該是所有組分及氣泡分布均勻穩(wěn)定。產(chǎn)生不均勻的情況有三種:一是骨料沉底、漿體上浮;二是漿體沉底、骨料上浮,這兩種情況即經(jīng)常遇到的混凝土離析;三是泌水即水分上浮逸出。綜上所述,混凝土拌合物產(chǎn)生泌水的直接原因是各組分密度不同導致沉降或上浮。
根據(jù)水分在混凝土中的存在狀態(tài),新拌混凝土中的水分可以劃分為結合水、潤濕水與自由水。水泥中反應速度快的部分在加水以后可能會發(fā)生水化反應,消耗部分水(結合水);水遇到干燥狀態(tài)的膠凝材料、骨料等以后,膠凝材料和骨料表面會吸附一定量的水,使干燥的材料濕潤,這部分水受到固體材料表面的吸附,不能逸出拌和物,但是可以被鄰近部位的水分置換,定義這部分水為潤濕水;新拌混凝土中其余的水分為自由水,在新拌混凝土中起潤滑的作用,混凝土坍落度在很大程度上取決于自由水量的多少和其潤滑效果,這部分水與固體材料的聯(lián)系較少,可以逸出混凝土,所有原材料中水的密度最小,逸出以后上浮,形成泌水,這部分水也稱為可泌水。
水分要從混凝土內(nèi)部泌出到表面,需要經(jīng)過較長的距離,猶如經(jīng)過彎彎曲曲的微細水管,最后到達表面。如果各種顆粒級配好,堆積密實,孔隙微細,則水分泌出需要經(jīng)過的距離很長,則會使泌水量減小。或者如果水分泌出的通道被阻斷,泌水量也會減小。
4.1.2泌水對混凝土性能的影響
泌水對混凝土強度的影響很有限,而對混凝土耐久性的影響至關重要。從泌水的機理可知,水分從混凝土內(nèi)部泌出到表面以后,在混凝土中形成了從內(nèi)到外的通道。這些通道首先降低混凝土的抗?jié)B透能力,雖然這些通道很難直接或通過儀器觀察到,但對于混凝土的抗?jié)B透性能影響很大,這一點對于有抗?jié)B透性能要求的高性能混凝土則非常重要。其次,泌水對混凝土的抗腐蝕能力、抗凍性能影響很大,原因同樣與泌水以后留下的通道有關,腐蝕性介質(zhì)通過泌水通道很容易進入混凝土內(nèi)部,到達鋼筋表面產(chǎn)生鋼筋銹蝕,或者直接與水化產(chǎn)物發(fā)生腐蝕反應;同樣通過泌水通道使得混凝土內(nèi)部很容易達到水飽和狀態(tài),高度飽和的混凝土在凍融循環(huán)作用下劣化的速度很快,產(chǎn)生凍融破壞。
4.1.3影響混凝土泌水的因素
混凝土的泌水幾乎與混凝土生產(chǎn)的所有環(huán)節(jié)有關,如膠凝材料、配合比、含氣量、外加劑、振搗過程等。
(1)水泥對混凝土泌水的影響
膠凝材料影響混凝土泌水主要與其反應活性、細度、顆粒形貌等有關。膠凝材料細度越高,比表面積越大,則濕潤膠凝材料表面所需的水量越多,即潤濕水量較多;同時如果膠凝材料較細,其反應活性增加,初期反應所需要的結合水也會增加。這兩部分水的增加會使可以逸出形成泌水的自由水量減少,從而對降低泌水有利。
(2)粉煤灰對泌水的影響
粉煤灰對混凝土泌水的影響具有兩面性。摻加粉煤灰減少混凝土泌水可以從三個方面理解:一是粉煤灰的顆粒小于水泥顆粒,比表面積較水泥大很多,因此對水分的吸附作用加強,因而可泌自由水減少;二是粉煤灰顆粒細小,混凝土中固相堆積密實度提高,混凝土中的孔隙細化,泌水通道減小,通道距離增加,也阻礙了水分泌出;三是粉煤灰的密度較小,相對于水泥顆粒而言,不易產(chǎn)生漿體沉降離析,拌和物經(jīng)時均勻性較好,有利于減少泌水。當然,粉煤灰對改善泌水的有利作用是在粉煤灰品質(zhì)較好的前提下。如果粉煤灰品質(zhì)較差,需水量增大,會使混凝土中可泌水量增大。
(3)配合比對混凝土泌水的影響
影響混凝土泌水的配合比因素主要有膠凝材料用量和砂率。膠凝材料用量增加或者砂率增加,會使拌和物顆粒的總比表面積增加,潤濕水分量增加,使可泌水量減少。同時,細顆粒用量增加,會使泌水通道長度增加,對減小混凝土泌水有利。膠凝材料用量增加,會使混凝土的粘聚性增加、保水性改善,對減少泌水有利。混凝土中的單位用水量與泌水有直接的關系,如果其他材料比例關系保持不變,用水量增加,會使新拌混凝土中的可泌自由水量增加,泌水增大。
(4)含氣量對泌水的影響
含氣量對新拌混凝土泌水有顯著影響。新拌混凝土中的氣泡由水分包裹形成,如果氣泡能穩(wěn)定存在,則包裹該氣泡的水分被固定在氣泡周圍。如果氣泡很細小、數(shù)量足夠多,則有相當多量的水分被固定,可泌的水分大大減少,使泌水率顯著降低。
(5)減水劑對泌水的影響
根據(jù)減水劑的作用機理,極性分子吸附在水泥顆粒周圍,使得顆粒之間相互排斥,減少絮凝作用,釋放被水泥顆粒包裹的水分,同時使水泥顆粒表面的吸附水層變薄,所需的潤濕水量大大減少。
(6)施工對混凝土泌水的影響
施工過程中影響混凝土泌水的主要因素是振搗,振搗過程中,混凝土拌和物處于液化狀態(tài),此時其中的自由水在壓力作用下,很容易在拌和物中形成通道泌出。另外,如果是泵送混凝土,泵送過程中的壓力作用會使混凝土中氣泡受到破壞,導致泌水增大。
4.1.4解決混凝土泌水的途徑
根據(jù)混凝土泌水的原理和各因素影響泌水的機理,解決混凝土泌水主要方法有以下幾種。混凝土配合比方面:適當增加膠凝材料用量,適當提高混凝土的砂率,在滿足其它性能的前提下,使混凝土適量引氣;在保證施工性能的前提下,盡量減少單位用水量。原材料方面:選用較細的摻合料和高品質(zhì)的引氣劑和顆粒級配好的骨料。減水劑方面:選用泌水較小的減水劑。如果配合比固定,在滿足標準和使用要求的情況下,選用減水率合適的減水劑摻量,避免減水率過高造成泌水。施工方面:嚴格控制混凝土振搗時間,避免過振。另外,對于新拌混凝土的性能控制,選取適當?shù)目刂泣c(如膠凝材料用量、水膠比、坍落度、含氣量以及混凝土的緩凝與灌筑速度控制等),使得控制有利于減小混凝土泌水。
4.2 遜強
4.2.1可能原因:
(1)混凝土拌合配料計量誤差超過允許值,尤其是膠凝材料和外加劑。
(2)水泥受過潮,或存放過期,強度等級已經(jīng)下降。
(3)骨料級配變化太大,尤其是含泥量超過規(guī)定范圍。
(4)遇下雨,骨料含水量大,而加水拌合時,未將其中的水扣除,使混凝土水灰比過大。
4.2.2注意避免:
(1)檢查拌合配料計量器具是否準確,特別是水泥及外加劑的計量。
(2)水泥保管時不得受潮。使用時按進貨批先到先用,并每批進貨時取樣進行凝結時間、安定性和強度復查檢驗,合格后才能使用。
(3)經(jīng)常檢查砂、石顆粒分布及含泥量情況,尤其是細粉末及泥土含量不得超過規(guī)定范圍,不符合者立即糾正。
(4)每日開工前,對砂、石料含水量進行測試,并換算施工配合比,遇下雨天或其它原因骨料含水量突變時,應及時測定,及時換算施工配合比。
4.3 混凝土拆模時發(fā)現(xiàn)表面脫皮
4.3.1可能原因:
(1)采用的脫模劑效果不好,或漏涂脫模劑;
(2)模板面原粘有灰渣,施工時未將其除掉即涂脫模劑;
(3)脫模過早,混凝土表面灰漿本身的抗拉強度還抵抗不過混凝土表面與模板的粘結力。
4.3.2注意避免:
(1)選用好的脫模劑,涂抹時一定要均勻,不能漏涂。
(2)灌筑混凝土前先將模板面的舊灰渣清除干凈,并涂好脫模劑再灌筑混凝土,避免舊灰渣粘在混凝土面影響光面。
(3)適當晚些拆模,待表面混凝土的抗拉強度增長到大于混凝土面與模板面的粘結強度才能拆模。
混凝土拆模強度掌握通過制取檢查試件與構件同條件養(yǎng)生試壓得出。
4.4 混凝土拆模時表面出現(xiàn)砂面或水印
4.4.1可能原因:
(1)混凝土灌筑搗固時,振動棒在混凝土內(nèi)緊靠模板振動時間過長,混凝土離析形成砂面。而在過振后振動棒靠著模板且向上拔出過快,滯留的氣泡與水在模板邊滾動形成水印。
(2)混凝土拌合物不均勻、有離析現(xiàn)象、凝固時間長并與灌筑速度沒有配合好、搗固工藝不規(guī)范至使混凝土向模邊泌水造成的。
4.4.2注意避免:
(1)混凝土搗固時,振動棒不要靠近模板,應離開模板20cm左右,振動棒垂直快速插入混凝土中,深度以30~40cm為宜,插入下層深度為5~10cm為宜。振搗過程中觀察振動棒周圍已不冒氣泡,剛冒出稀漿為度,然后慢慢拔出振動棒,將棒底滯留的氣泡引出混凝土外。
(2) 混凝土混合料拌合要均勻,一般有效攪拌時間應不少于3min,才能充分拌勻摻合料和發(fā)揮減水劑的作用。如用攪拌輸送車運送混凝土拌合物,途中運輸車攪拌時間超過30 min,,即混凝土拌合物在拌合機的攪拌時間可以縮短,但不少于2 min。
采用插入式振動器其振搗棒距模板應控制在20cm,混凝土入模(每層)搗固前應將混凝土拌合物鈀平,并使模板邊周圍的混凝土比中間稍高出10cm左右,然后再振搗,每處振搗的時間不宜過長,不使混凝土離析。
每層混凝土振搗過后要用搗固鏟沿模板插邊,把水泥漿引到模邊并將模邊滯留的氣泡排出。
4.5 混凝土表面出現(xiàn)“黑斑”和“云彩”狀
4.5.1可能原因:
(1)此情況與使用的脫模劑有關。當采用機油作脫模劑,如涂得很合適,機油在模板面只起潤滑作用,灌入混凝土時,被混凝土表面水泥顆粒周圍的水膜隔離,即成為良好的水泥與模板隔離劑。如機油涂得過多,由于新灌入的混凝土在模板邊流動將多余的機油往前排,當混凝土停止流動時,此處就形成一道機油圍堰,由于機油積得很厚,即浸入水泥漿體中與水泥中的鈣離子發(fā)生反應形成一種黑色物質(zhì),機油越多其色質(zhì)越黑。
(2)模板合縫不嚴密。當模板有漏漿時,混凝土表面即出現(xiàn)沙面,即使是不漏漿,僅僅滲水,在滲水部位的混凝土表面就形成“黑斑”。
4.5.2注意避免:
(1)盡量不用機油作為混凝土隔離劑,改用其它不與水泥發(fā)生反應的油質(zhì)作隔離劑,或購置成品的優(yōu)質(zhì)脫模劑。如需要用機油作隔離劑,也不要用純機油,應摻些其它不與水泥發(fā)生反應的油質(zhì)稀釋。涂涮時力求越薄越好。
(2)模板合縫必須嚴密,不得有滲水、漏氣,更不得有漏漿現(xiàn)象。
4.6 混凝土表面氣泡多
4.6.1可能原因:
往往在混凝土下彎曲部位的表面氣泡多,這部位的混凝土外表面正好是模板面偏上方,振搗時氣泡趁混凝土液化上升遇到模板阻擋,如振動工藝和掌握的時間不適當,氣泡即滯留在模板邊,拆模時混凝土表面氣泡就多。
4.6.2注意避免:
灌筑混凝土時,按每層灌厚不大于30cm搗固一次,振搗前應用布料工具(如鐵鈀等)將混凝土鈀平后再振搗。振搗時,振搗器應距模板20cm左右,垂直快速插入混凝土內(nèi),每在一個位置上的振動時間,以混凝土正好泛漿為度。振搗器拔出混凝土時速度要慢,保證振動棒周圍的空氣能夠跟隨振動棒引出。并在混凝土剛振搗過后趁模邊混凝土稀漿液化時立即用搗固鏟順模板邊插搗一遍,然后人工用搗固錘距模板2~3cm,插入深20~30cm上下晃動混凝土數(shù)下效果更好。
第五章 結論
5.1在混凝土中摻加摻合料可節(jié)約大量的水泥和細骨料:在一般情況下,在混凝土中合理使用一噸摻合料可以取代0.6-0.9噸的水泥,并取代10%左右的細骨料。
5.2減少了用水量:經(jīng)實驗,用30%的摻合料代替20%~25%的水泥,攪拌混凝土中用水量可減少5%~7%左右,而且增強了混凝土的密實性。
5.3改善了混凝土拌和物的和易性:摻合料改善混凝土拌和的和易性的效果比較顯著,對于貧混凝土和細集料用量不足的混凝土特別有效。
5.4增強混凝土的可泵性:對于摻加摻合料的泵送混凝土來說,出了因改善和易性而提高了易泵性之外,同時由于泌水性和離析現(xiàn)象改善,以及摻合料本身的效應,可以得到更好的減阻效果。
5.5減少水化熱、熱能膨脹性:混凝土中水泥水化反應要放出熱量,在大體積混凝土構件中會出現(xiàn)中心與邊緣溫度差而產(chǎn)生應力,導致裂縫。由于摻合料的摻加有利于減少在混凝土內(nèi)部由于水化熱而產(chǎn)生的升溫,減少了混凝土熱膨脹出現(xiàn)裂縫的危險。
5.6提高混凝土抗?jié)B能力:由于混凝土能減少用水量和降低水灰比,并且在和水泥水化過程中析出氫氧化鈣生成水化硅酸鈣和水化鋁酸鈣凝膠,使水泥石中毛細孔的數(shù)量減少,孔徑變小,增加了對液體和氣體的滲透和擴散作用的抵抗力,即抗?jié)B力。試驗證明:混凝土水膠比0.40以下,摻摻合料達25%以上的混凝土,56d電通量均低于1500C。
更多關于材料方面、材料腐蝕控制、材料科普等方面的國內(nèi)外最新動態(tài),我們網(wǎng)站會不斷更新。希望大家一直關注中國腐蝕與防護網(wǎng)http://www.ecorr.org
責任編輯:王元
投稿聯(lián)系:編輯部
電話:010-62313558-806
中國腐蝕與防護網(wǎng)官方 QQ群:140808414
免責聲明:本網(wǎng)站所轉載的文字、圖片與視頻資料版權歸原創(chuàng)作者所有,如果涉及侵權,請第一時間聯(lián)系本網(wǎng)刪除。
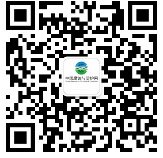
官方微信
《中國腐蝕與防護網(wǎng)電子期刊》征訂啟事
- 投稿聯(lián)系:編輯部
- 電話:010-62316606-806
- 郵箱:fsfhzy666@163.com
- 中國腐蝕與防護網(wǎng)官方QQ群:140808414