前兩篇文章我們講到了金屬的腐蝕機理及金屬在海水中的耐蝕性,本篇文章我們來專門談一下鋼鐵的耐蝕及如何增強鋼鐵的耐蝕性。
在第一篇文章中講到,在自然界中,金屬的大部分腐蝕是屬于電化學腐蝕,兩種不同金屬連在一起處于一種導電液體中,在兩個金屬之間就會形成電流由電勢高的金屬流向電勢低的金屬,而0.
三種,一是提高鋼鐵本身的電極電位,二是增強鋼鐵的鈍化效應,三是盡量讓鋼鐵形成單一的微觀組織。
01 高金屬的電電位
當鉻元素加入鐵中形成固溶體時,鐵固溶體的電極電位能得到顯著提高,當鉻的含量達到2/8、2/8、3/8…..鉻/鐵摩爾比時,鐵的電極電位就發(fā)生跳躍式的增高,腐蝕亦跳躍式地減弱。這一規(guī)律稱之為n/8規(guī)律,如當鉻/鐵比為1/8(12.5%)時,可使鐵的電位由-0.56V躍升至0.2V,可使鋼在大氣等弱腐蝕性介質(zhì)中具有較好的耐蝕性。12.5%摩爾比也是作為不銹鋼的最低含鉻量要求,這也是為什么所有不銹鋼的鉻含量均大于11 wt%,如下表1幾種常見不銹鋼的化學成分。
表1 幾種常見不銹鋼的主要化學成分
02 金屬易于鈍化
大多數(shù)金屬除了金子外,當暴露于水和氧氣時,經(jīng)歷了稱為電化學的電化學氧化反應.這個過程會導致氧化層形成和覆蓋金屬表面。在鋼中,該氧化物層是水合鐵(III)氧化物,通常稱為生銹.在許多金屬包括鋼鐵,氧化層很脆不致密,很容易剝落,從而使更多的金屬暴露在空氣和水中,從而產(chǎn)生更多的銹。這種持續(xù)的循環(huán)逐漸消耗和惡化金屬。
然而,在特定金屬中,該氧化物層耐用并且緊密地粘附到表面上,從而形成保護屏障。這種保護屏障用作阻擋空氣和水分的侵入的屏蔽,從而防止進一步腐蝕。已知三種提供屏障保護的金屬氧化物是氧化鋁,氧化鉻和二氧化硅。
向鋼中加入鉻、鋁、硅等元素,可在鋼表面生成Cr2O3、Al2O3和SiO2等致密的鈍化膜,起到防腐的作用。其中鉻是最有效的元素。主要耐蝕元素的作用如表2所示。
表2 主要耐蝕元素的作用
例1 Cor-Ten鋼
Cor-Ten鋼是一種耐候鋼,即耐大氣腐蝕鋼,是介于普通鋼和不銹鋼之間的低合金鋼系列,耐候鋼由普碳鋼添加少量銅、鎳等耐腐蝕元素而成,耐候性為普碳鋼的2-8倍。具體見《成也蕭何,敗也蕭何---銅在鋼鐵中的作用》。
例2 原油油船貨油艙耐蝕鋼
目前針對油船貨油艙腐蝕所采取的防護措施主要有:加注緩蝕劑、采用防腐涂層和耐蝕鋼板。其中,加注緩蝕劑過程復雜,長期投資高;防腐涂層使用過程中存在嚴重的局部腐蝕隱患,每2.5a就須對油船進行涂層維護和重新涂布,需要耗費高額成本,延長工期,并且貨油艙空間封閉,施工環(huán)境惡劣,也會一定程度上影響施工質(zhì)量。
圖 1 油船貨油艙上下底板
1995年,國際海事組織對油船貨油艙用耐蝕鋼提出推薦性要求,并推薦各國進行研究。2010年5月14日,國際海事組織海上安全委員會(MSC)第87次會議正式通過了《原油油船貨油艙防腐保護替代方法性能標準》,并于2012年1月1日生效。2013年1月1日及以后簽訂建造合同或2016年1月1日及以后交付的所有5 000t級以上油船必須從貨油艙保護涂層和耐蝕鋼方案中選擇采用一種。該性能標準附件中對耐蝕鋼的適用范圍、目標壽命、試驗程序及性能標準做了規(guī)范和要求。標準規(guī)定耐蝕鋼的目標使用壽命是25a,對耐蝕鋼的要求是在貨油艙頂腐蝕環(huán)境中,鋼材25a后估計腐蝕損耗值(ECL)不超過2mm; 在艙底腐蝕環(huán)境中,年均腐蝕速率(C. Rave)不超過1.0mm/a。兩種環(huán)境均要求焊縫處放大1000倍后,母材和焊縫金屬之間不出現(xiàn)階梯狀不連貫表面。
對于耐蝕鋼開發(fā),目前走在前列、技術較成熟的國家是日本。早在1999年,日本造船協(xié)會的SR242項目組利用實船測試、實驗室模擬等手段對超大型油船(VLCC)進行了為期3a的研究,成功揭示了貨油艙內(nèi)的腐蝕狀況、腐蝕機理及過程。
圖 2 NSGP-1點蝕的數(shù)量為傳統(tǒng)鋼的1/15
基于上述研究,日本新日鐵、JFE、住友金屬三大鋼鐵公司分別開發(fā)了新型油船貨油艙用耐蝕鋼。新日鐵開發(fā)了NSGPTM-1 和NSGPTM-2兩種耐蝕鋼。2003 年新日鐵公司與NYK公司合作首次成功開發(fā)了新型耐蝕鋼NSGPTM-1。表3給出了NSGPTM-1 鋼的化學成分。從表3可知,其所含合金元素較少,成分與傳統(tǒng)船用鋼AH32 差別不大,完全符合IACS標準,但其中銅、鎳、鉻及鉬的配比必是非常考究以致發(fā)揮了優(yōu)異的耐蝕性能。將NSGPTM-1 鋼應用在三菱重工建造的“TAKAMINE”號巨型油船貨油艙下底板,該船運營2.5a后的考察結(jié)果表明,使用NSGPTM-1 鋼的貨油艙下底板最大腐蝕孔只有2.8mm,而采用傳統(tǒng)鋼板的則為6.3 mm。依據(jù)國際慣例,腐蝕孔超過4 mm 需要重新涂裝船體,超過7 mm則需要焊接維修。2008 年,新日鐵公司與NYK 公司又開發(fā)了應用于油船貨油艙上甲板的耐蝕鋼NSGPTM-2,經(jīng)過5a年的實船試驗,檢測結(jié)果表明,NSGPTM-2鋼5a平均腐蝕速率小于0.07 mm/a,比傳統(tǒng)鋼降低了38%。
表3 NSGPTM-1 鋼的化學成分
03 鋼獲得單相組織
不銹鋼的基體組織是獲得所需要力學性能和良好耐蝕性的保證,使鋼在室溫下獲得單相的組織,如單相鐵素體和單相奧氏體就可以減少微電池數(shù)目,這樣鋼的耐蝕性就得以提高。
04 含量、組織和雜質(zhì)的影響
鋼中碳含量和鋼的組織對鋼的耐蝕性有明顯影響。碳含量增大,組織中碳化物陰極相增多,微電池的作用增大而降低耐蝕性。降低碳含量可提高鋼的耐蝕性,但鋼中碳含量降低、強度降低,需通過合金化來提高強度。
鋼中的雜質(zhì)對鋼的性能包括耐腐蝕性能有明顯的影響,降低鋼中的雜質(zhì)是提高鋼性能的有效方法。磷、硫、氧是鋼中主要的有害雜質(zhì),對于鋼的力學性能來說,S,P,O含量越低越好。S對鋼的耐蝕性不利,耐蝕性隨著雜質(zhì)S含量的提高而惡化,其影響主要與鋼中的非金屬夾雜物有關。對于耐蝕性來說,適當?shù)腜對耐蝕性有一定的益處,P與Cu元素配合能夠改善鋼的耐大氣腐蝕性能,能一定程度地改善耐海水腐蝕性。
表 4 碳及雜質(zhì)元素對鋼的耐蝕影響
總結(jié)
不銹鋼耐蝕性主要是含有大量的鉻,遵循n/8規(guī)律
少量的Cu-P、Cu-P-Cr、Cu-P-Cr-Ni 組合也可提高碳素鋼或低合金鋼的耐蝕性,如耐候鋼或貨油艙耐蝕板
單相組織利于耐蝕性的提高
碳及硫含量會促進鋼鐵的腐蝕
參考文獻
1. 張國宏,成林,李鈺. 海洋耐蝕鋼的國內(nèi)外進展,中國材料進展,2014,33(7)
2. www.nipponsteel.com
免責聲明:本網(wǎng)站所轉(zhuǎn)載的文字、圖片與視頻資料版權歸原創(chuàng)作者所有,如果涉及侵權,請第一時間聯(lián)系本網(wǎng)刪除。
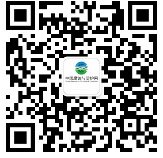
官方微信
《中國腐蝕與防護網(wǎng)電子期刊》征訂啟事
- 投稿聯(lián)系:編輯部
- 電話:010-62316606-806
- 郵箱:fsfhzy666@163.com
- 中國腐蝕與防護網(wǎng)官方QQ群:140808414