詳解航空發動機的“防護服”-熱障涂層
2023.05.20-2023.05.31全國科技周活動--中國腐蝕與防護學會
新代次戰斗機上渦輪前進口溫度已接近2000K,得益于航空發動機的三大隔熱防護技術:單晶合金、氣膜冷卻和熱障涂層技術。在面對高達2000K的進口溫度時,要讓單晶工作在1100-1150℃,僅僅采用氣膜冷卻是遠遠不夠的。當氣膜冷卻效果達到極限后,熱障涂層便承擔了所有,因此熱障涂層被稱為航空發動機最重要的“防護服”。本期科技周,小編就為您送上關于熱障涂層的科普盛宴。
熱障涂層是什么?
眾所周知,渦輪前溫度是現代航空發動機關鍵指標之一,這個渦輪指的是高壓渦輪,航空發動機屬于熱機,能量來源于空氣受熱膨脹,從能量守恒角度來講,燃氣溫度越高,產生的能量越大,但是航空發動機燃氣溫度有一個限制,那就是高壓渦輪承受能力,噴氣式發動機工作需要空氣由壓氣機送入燃燒室,而高壓壓氣機由高壓渦輪帶動,因此高壓渦輪需要承受高溫高速燃氣帶來的沖擊,還要高速旋轉帶動高壓壓氣機,對于材料要求極高,所以高壓渦輪與燃燒室、高壓壓氣機被稱為發動機“核心機”三大件就是這個原因。
渦輪前溫度是現代航空發動機關鍵指標
現代航空發動機高壓渦輪普遍采用鎳基高溫合金,它的最高工作溫度大約是1100度,四代航空發動機渦輪前溫度已經達到1600度,抵達材料表面溫度也有1100度,在這樣高溫度下材料會變軟,無法承受高速運動產生的應力,實際上未來發動機燃氣溫度有可能超過2000度,抵達材料表面溫度在1500度以上,僅憑鎳基高溫合金本身已經不能適應要求。因此,材料科學家不斷探索著提升渦輪抗高溫能力的方法,其中最有效的方法就是穿上“防護服”—在渦輪部件上涂覆具有不同功能的涂層,從而達到提高使用性能、使用更可靠以及延長使用壽命的目的。
從用途上來看,發動機的“防護服”通常有以下幾類:抗氧化和防熱腐蝕的涂層,放置葉片間斷劃傷內腔的耐磨涂層,填補部件組合除細小縫隙的封嚴涂層,以及在葉片表面起到隔熱作用的熱障涂層。
熱障涂層常用于高溫防護,是近年來涂層研究領域的熱點之一。熱障涂層有很多優點,它能降低零部件的工作溫度,從而降低因工作疲勞帶來的損傷,同時,熱障涂層也可以減少渦輪葉片對冷卻氣體的需求量,有助于提高發動機工作效率,延長工作壽命。
熱障涂層擁有一個像“三明治”一樣的多層結構,由陶瓷隔熱層、金屬粘結層和高溫合金底層組成涂層系統。盡管形似“三明治”,但熱障涂層的制備并不是簡單地層層疊加,需要先將制備涂層的材料蒸發成蒸汽或細化成直徑微米級的顆粒,再通過結晶生長或借助極高的能量,將這些顆粒牢固地涂覆在材料表面。因此,熱障涂層常使用電子束物理氣相沉積、等離子體噴涂等工藝制備。
熱障涂層結構
熱障涂層應用及研究現狀
熱障涂層技術起源于19世紀70年代。1976年,在美國NASA劉易斯研究中心,陶瓷熱障涂層在J75渦噴發動機渦輪葉片上試驗成功。到20世紀90年代,熱障涂層技術迎來快速發展。美國的GE公司在20世紀90年代后期開發出新型單晶合金基體熱障涂層。GE90發動機葉片采用這種熱障涂層后,性能較未采用涂層的葉片相比大大提高。90年代后,熱障涂層技術逐漸得到廣泛應用。英國的RR公司在20世紀90年代以來逐漸將熱障涂層大量應用到軍用和民用發動機上。其中,著名的遄達系列發動機就使用了熱障涂層。
高壓渦輪
現代航空發動機高壓渦輪熱障涂層主要采用陶瓷材料,陶瓷優點就是熔點高、強度大、熱導率低,傳統發動機熱障涂層多采用氧化鋯基(YSZ)陶瓷材料,它可以使材料承受的溫度降低100度,這樣加上鎳基高溫合金本身1100度,再加上氣膜冷卻技術還能提供400度左右的冷即效果,那么航空發動機渦輪前溫度可以達到1600度左右。這個溫度正是第四代航空發動機F119渦扇發動機渦輪前溫度。YSZ具有低的熱導率和相對較高的熱膨脹系數,但是它在使用過程中存在如下問題:
(1)當工作溫度高于1200℃時,隨著燒結時間延長,YSZ 的孔隙率和微觀裂紋數量逐步減少,從而導熱系數上升,隔熱效果下降。
(2)高溫環境中,熱障涂層的面層和粘接層之間會生成以含鋁氧化物為主的熱生長氧化物(TGO),同時金屬粘接層會產生“貧鋁帶”,隨著熱循環次數的增加,貧鋁帶擴大,富 Ni、Co的尖晶石類氧化物在TGO 中形成,從而使 TGO 內部產生較大的應力,最終誘發裂紋并導致陶瓷面層脫落。
(3)YSZ 陶瓷面層、金屬粘接層、TGO 的熱膨脹系數存在的差異會引起致YSZ陶瓷面層/TGO界面、TGO/金屬粘接層界面上在從工作溫度(上千攝氏度) 降到室溫的過程中產生應變失配,從而形成熱失配應力,最終會導致YSZ 面層脫落。
(4)航空發動機熱障涂層的 CMAS腐蝕
高溫腐蝕也是是熱障涂層失效的一個重要原因。航空飛機執行任務的實際工況中,發動機會攝入大量沙塵、火山灰、跑道碎屑以及各種環境污染物,這些吸入物在高溫下附著于發動機熱端部件(如渦輪葉片、燃燒室壁等);研究發現沉積物的成分主要為CaO、MgO、Al2O3和SiO2,簡稱CMAS。CMAS的熔點隨成分變化而變化,但一般來說,當工作溫度超過1200℃時,CMAS即開始熔化,高溫熔體會沿著葉片表面TBCs中微裂紋、孔隙內滲,同時與涂層組分反應,造成涂層相成分和微觀結構破壞,加速涂層失效,使得葉片合金直面高溫燃氣,損害發動機性能。
高溫下CMAS (CaO、MgO、Al2O3和SiO2)對熱障涂層的破壞
關于環境沉積物腐蝕的認識和研究最早見于Smialek等人在《波斯灣戰爭中渦輪翼型的退化》的報道。他們發現當一個地區的空氣沙塵濃度較高、霧霾多發時,在此地區服役的直升機的發動機葉片上存在玻璃狀沉積物,并認識到它對航空發動機運行的潛在危害。Toriz等人在1988年國際燃氣輪機和航空發動機會議和博覽會上指出在渦輪導向葉片中應用的TBC需要面臨極其惡劣的服役環境,其失效主要原因是熱循環、粘結層的氧化以及一些固體顆粒的沉積引發的腐蝕。為研究失效過程和機理,他們收集了一個飛機發動機葉片,這架飛機長期飛行于沙塵濃度較高的國家。研究發現,高于1200℃時,這些沉積物就會熔化并撞擊在葉片表面,熔融的碎片可以進入多孔TBC結構,并腐蝕涂層,或者通過熱失配引起應力增加,從而減少涂層的熱循環壽命。Stott等人在《熱障涂層在高溫下的降解》文章中研究了服役于熱帶沙漠氣候地區的飛機發動機沉積物后指出:沉積物是一種具有透輝石型結構的鈣鎂鋁硅酸鹽玻璃,YSZ TBC在1300~1600℃的溫度下易受熔融砂和玻璃碎片的腐蝕,其精確機理受熔體組成的影響:含Ca量較低的沉積物腐蝕過程主要消耗穩定劑Y2O3;含Ca量較高的沉積物會消耗Y2O3和ZrO2造成相轉變。由于這些沉積物的存在會導致飛機發動機葉片的失效,嚴重危害飛機服役的安全性。
為了改善熱障涂層性能,人們進行了大量的探索和研究。下表是影響 YSZ 涂層服役壽命的常見問題及其改善需求、改善方法。
1、改善抗燒結性
(1)提高陶瓷涂層純度,減少 YSZ 涂層中 SiO2和 Al2O3雜質的含量,可以顯著降低涂層的燒結速率,平面收縮傾向減小,從而降低導熱系數的增加速率,涂層表現出一定的抗燒結性。
(2)在涂層中添加特殊化學元素。例如在鑭系鋯酸鹽體系( La2Zr2O7)涂層中適量摻雜Hf 、Nd、Gd、Sm 等元素能夠有效提升涂層的抗燒結性能。
2、控制 TGO 的生長
航空發動機在高溫服役過程中,粘接層Al,Cr,Ni 等金屬元素接觸氧氣發生選擇性氧化,會在粘接層(BC)和頂層陶瓷層(TC)表面形成一層熱生長氧化物(TGO) ,進而造成涂層局部膨脹并對TC 產生張力,當張力超過了TC的結合力時就會引起裂紋擴展,直至表面涂層的剝落。
(1)改變粘接層的化學成分。適當摻雜一些活性元素( 如 Y,Hf,Zr),在這些元素的偏析聚集作用下,降低Al2O3的增長速度,抑制TGO 生長;(2)采用冷噴涂( CS)、超音速火焰噴涂( HVOF)等工藝或預先沉積一層富 Al 的PVD “薄夾層”,改善涂層結構,降低氧氣擴散系數,從而減緩 TGO 的生長速度。
3、改善抗CMAS腐蝕性能
發動機葉片上 CMAS 的形成不僅會造成釔的損耗引起 ZrO2熔融相變產生不穩定相,CMAS 的沉積還會引起涂層應力增大,加速涂層剝蝕,大大降低熱障涂層的服役壽命。研究發現從以下幾方面可改善涂層抗 CMAS 腐蝕性能:
(1)改變涂層化學成分。在 YSZ 中添加 Al,Ti,Si等元素可誘導生成一種氧基磷灰石相,從而抑制 CMAS 的向涂層內部侵蝕,降低界面層的浸潤性能,增強涂層抗 CMAS 性能。
(2) 改變涂層結構。燒綠石結構的 Y2Zr2O7中滲入的 CMAS就比一般結構的 YSZ 少很多。對于“ YSZ 內層 + 稀土鋯酸鹽( Ln2Zr2O7) 燒綠石外層”、“YSZ +Sm2Zr2O7 ”和“YSZ +Gd2Zr2O7 ”等雙層熱障涂層,由于燒綠石外層可以減少 CMAS 的滲入,因此熱障涂層的抗 CMAS 侵蝕性得到極大提高。
4、改善YSZ 面層應變容限
采用EB-PVD 技術、等離子物理氣相沉積技術(PS-PVD)、懸浮液等離子噴涂技術(SPS)等可制備 “柱狀”結構的 YSZ 陶瓷面層,通過柱間縱向開裂釋放陶瓷面層/TGO 界面上的熱失配應力,使熱障涂層可以承受更高的失配應變,從而提高YSZ 陶瓷層應變容限,延長涂層熱循環壽命。這種方法工藝簡單,成本低,但是縱向裂紋是通過表面集中加熱的方式產生的,密度不高且形態無法控制,因此涂層的循環壽命不穩定,使得涂層在應用上受到很大的限制。
新型熱障涂層發展方向
尋找新材料來滿足更高的發動機出口溫度是熱障涂層制備和發展的重要方向。為了得到理想的熱障涂層,必須獲得具備更低熱導率的頂層陶瓷層,開發出新型低熱導率熱障涂層和陶瓷基復合材料熱障涂層成為研究熱點。
1 、新型低熱導率熱障涂層
提高熱障涂層的熱阻需要從降低熱導率入手,熱障涂層中的熱量傳輸主要有電子傳導、熱輻射和晶格聲子傳導三種方式,因此降低聲子平均自由程、聲子速度或材料密度,能夠有效減少晶格聲子的熱量傳輸。材料本身固有的缺陷以及摻雜都可以顯著提高外在缺陷散射,從而降低材料的導熱性能。
(1)改變涂層化學成分
利用Y2O3摻雜 ZrO2、各種鑭系元素( 包括 La,Gd,Er,Nd,Dy 和Yb)單獨或共摻雜ZrO2、過渡金屬元素( 如 Ni,Nb 和 Ta)摻雜以及Hf摻雜ZrO2,誘導晶格應變,從而增大晶格的非簡諧振動和聲子散射,進而降低材料熱導率。
(2)改善涂層晶體結構
燒綠石結構體系(A2B2X7)憑借其較低的熱導率近幾年來成為新型熱障涂層研究熱門。例如稀土鋯酸鹽 Ln2Zr2O7(Ln 為稀土元素)燒綠石結構陶瓷涂層(如Gd2Zr2O7,Sm2Zr2O7)相比于YSZ,具有更好的熱物性和良好的機械性能。結構相似的鑭系鋯酸鹽摻雜時,因其可以形成固溶體,也能夠降低材料的熱導率。而La2Hf2O7的熱導率比La2Zr2O7更低。此外,增加涂層孔隙率也有利于降低涂層熱導率。
2、陶瓷基復合材料熱障涂層
高溫金屬材料(如鎳、鈷或鐵基超合金) 常被用于制作渦輪發動機的葉片等,但是它們通常在超過其熔點溫度的環境下服役,所以熱穩定性得到極大挑戰。由于陶瓷基復合材料(CMC)能夠承受1250 ℃以上的高溫,因此能夠承受更高溫度的新型CMC復合材料成為下一代航空發動機高溫部件的主要候選材料,從而提高發動機熱端部件的服役溫度,保障發動機的功率和轉換效率。
CMC 材料不同于金屬材料,制成的熱端部件在工作時不需要進行氣冷,并且還能改進零件的耐久性,從而極大地提高發動機的推力和工作率。2013年,羅羅公司采用 SiC/SiC 復合材料制造成發動機高壓渦輪葉片進行試驗,結果顯示,葉片質量可減少50% 左右。但是,CMC 在高溫下的氧化燒蝕限制了其在飛機上的應用。以 SiC-纖維/SiC-基體 CMC 材料為例,在高壓渦輪機的高溫氧化條件下,會形成一層SiO2保護層來阻止 CMC 繼續被氧化,但是 SiO2層又會與水蒸氣反應生成氫氧化物,從而導致 CMC 中 SiC基體的侵蝕。在 CMC 基體上制備一層環境熱障涂層( EBC) 是解決這一問題的關鍵。
環境熱障涂層構成
EBC 通常由粘接層、過渡層和頂層三部分構成(如上圖所示)。粘接層一般由 Si 元素組成,主要作用是確保 EBC 和 CMC 基體結合良好; 過渡層一般由鋇鍶鋁硅酸鹽(BSAS)和莫來石混合而成,主要起抗高溫氧化和抑制與水蒸氣反應的作用; 頂層由 BSAS 構成,主要起到抗高溫腐蝕和抗外來物沖擊的作用。
3、熱障涂層的CMAS腐蝕防護方法
由于CMAS引起TBCs損傷和失效的原因非常復雜,因此針對CMAS腐蝕的防護方法也各不相同。Rai等人較早總結了TBCs的3種CMAS腐蝕防護方法,可分為:非滲透性涂層、犧牲性防護涂層以及多層復合的防護涂(通常是非滲透性涂層、犧牲性涂層以及不潤濕涂層的復合涂層)。非滲透性涂層是一種致密、無裂紋、無孔的層,包括氧化物、非氧化物或金屬涂層等,沒有反應過程;而犧牲性防護涂層內某些成分會與環境沉積物反應,生成更難滲透的物質;不潤濕的防護層著重改進涂層的表面質量,使熔融的物質無法潤濕涂層表面,從而減緩了熔體滲透。這3種方法旨在減緩CMAS的滲入和化學反應以及減少CMAS在表面的附著,本質上是在表面制備一層防護層,直接阻擋CMAS滲入,屬于物理方法。同時,近年來出現了很多其他抗CMAS的腐蝕方法,比如:改性YSZ涂層(促使環境沉積物結晶或與其反應直至消耗完沉積物)、新型的熱障涂層材料和TBC的結構設計。以上所述的方法各有優劣,但改性YSZ涂層和開發新型熱障涂層體系的方法更受研究者青睞,更具發展潛力。
免責聲明:本網站所轉載的文字、圖片與視頻資料版權歸原創作者所有,如果涉及侵權,請第一時間聯系本網刪除。
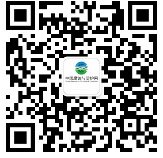
官方微信
《腐蝕與防護網電子期刊》征訂啟事
- 投稿聯系:編輯部
- 電話:010-62316606
- 郵箱:fsfhzy666@163.com
- 腐蝕與防護網官方QQ群:140808414