微弧氧化(MAO)是在電解質(zhì)溶液中利用熱化學(xué)、等離子體化學(xué)以及電化學(xué)方法在Al、Mg、Ti等金屬及其合金表面,通過產(chǎn)生火花放電而生成一種陶瓷膜層的方法,與化學(xué)轉(zhuǎn)化、電鍍、化學(xué)鍍以及有機(jī)涂裝等表面防護(hù)技術(shù)相比,MAO技術(shù)所制備的膜層具有優(yōu)異防腐抗磨性能,引起了科學(xué)界濃厚的研究興趣和工程界對應(yīng)用開發(fā)的極大關(guān)注。MAO屬于一種多因素控制技術(shù),處理過程中將會受到諸如能量參數(shù)(包括電流密度、電壓、頻率、占空比及處理時(shí)間)、溶液特性(包括溶液成分、濃度、溫度、電導(dǎo)率及pH值)及基體合金元素等多種因素的影響,并伴隨化學(xué)、電化學(xué)、熱化學(xué)以及等離子化學(xué)反應(yīng)。因此,除了工藝和機(jī)理研究的復(fù)雜性外,涂層質(zhì)量以及工程應(yīng)用的可控性,都使該技術(shù)面臨重重困難。迄今為止,學(xué)者們的研究內(nèi)容主要包括:(1)MAO機(jī)理;(2)電源特性、工作模式、電參數(shù)及氧化時(shí)間;(3)電解液組成、溫度、電導(dǎo)率、pH值及電解質(zhì)濃度;(4)鎂合金基體組成、結(jié)構(gòu)及前處理;(5)MAO膜后處理。相關(guān)研究動(dòng)態(tài)和進(jìn)展在文獻(xiàn)中都有綜述,本文將從以上幾個(gè)方面就MAO技術(shù)及其在鎂合金表面防護(hù)領(lǐng)域的研究動(dòng)態(tài)進(jìn)行簡要綜述,供同行參考。
1 微弧氧化
1.1MAO發(fā)展歷程
MAO發(fā)展歷程的示意圖如圖1所示。早在1880年,前蘇聯(lián)科學(xué)家Sluginov等就已經(jīng)發(fā)現(xiàn)了浸入電解液中的金屬通電后會產(chǎn)生發(fā)光現(xiàn)象。但直到1923年,有專利記載Dunstan等開始在鉻酸鹽溶液里對Al及鋁合金進(jìn)行陽極氧化處理 (Mg及其合金的陽極氧化處理研究滯后約10年)。1932年,德國科學(xué)家Günterschulze和Betz[9]的研究揭示了浸入電解液中的金屬在高電場下會出現(xiàn)火花放電現(xiàn)象,但也指出火花對氧化膜具有破壞作用,從而認(rèn)為“制備涂層的電壓不應(yīng)高于火花電壓”,這在一定程度上限制了對該現(xiàn)象的深入研究。雖然在1941年和1947年的授權(quán)專利中提出使用大電流密度在酸性溶液中對Mg及其合金進(jìn)行陽極氧化處理的方法,但有研究者認(rèn)為MAO開始研究的時(shí)間應(yīng)以20世紀(jì)60年代美國科學(xué)家McNeil和Gruss利用這種陽極火花放電現(xiàn)象在金屬表面沉積金屬氧化物涂層為標(biāo)志。著名的Mg及其合金陽極氧化工藝,如Cr-22、Dow17以及HAE,就是在這一時(shí)期報(bào)道的。
隨后,美國Illinois大學(xué)Brown課題組、前蘇聯(lián)科學(xué)家Markov課題組和德國Karl-Marx-Stadt工業(yè)大學(xué)Kurze課題組先后開始了Al、Mg、Ti、Zr等閥金屬表面火花放電沉積涂層的研究,并將這一方法分別命名為陽極火花沉積 (ASD)、MAO和火花放電陽極氧化 (ANOF)。20世紀(jì)80年代后,MAO技術(shù)已經(jīng)成為美、德、俄、日等國家研究的熱點(diǎn),并將此項(xiàng)技術(shù)從實(shí)驗(yàn)室研究轉(zhuǎn)向工業(yè)應(yīng)用。20世紀(jì)90年代后,我國學(xué)者才逐步開展MAO相關(guān)技術(shù)研究,進(jìn)一步豐富了MAO技術(shù)及其在金屬表面處理領(lǐng)域的潛在應(yīng)用,對該技術(shù)的發(fā)展和推廣起到了很大的推動(dòng)作用。
此外,根據(jù)液相等離子體的放電現(xiàn)象和作用原理,MAO還被稱作等離子體電解氧化(PEO)、微弧放電氧化(MDO)、微等離子體氧化 (MPO)。從發(fā)表文獻(xiàn)量來看,使用MAO和PEO兩種名稱的文獻(xiàn)居多。由于MAO只是等離子體氧化過程中電壓較高時(shí)微弧放電的一個(gè)階段,該名稱叫法不妥,所以很多學(xué)者更青睞于PEO這個(gè)名稱,但國內(nèi)普遍使用“MAO”這一名稱。
1.2 MAO過程及其機(jī)理
MAO過程中的實(shí)驗(yàn)現(xiàn)象、電壓及電流之間的關(guān)系如圖2所示。MAO的基本工藝過程包括:鈍化階段、陽極氧化階段、火花放電階段、MAO階段和弧光放電 (或熄弧) 階段。在臨界擊穿電位U3之前,材料表面依次發(fā)生普通鈍化、普通陽極氧化,形成一層薄的絕緣氧化膜;當(dāng)施加電壓高過擊穿電位U3后,絕緣氧化膜被擊穿,材料表面出現(xiàn)無數(shù)細(xì)小的白色火花,即為火花放電階段。當(dāng)電壓繼續(xù)增加至U4時(shí),表面會出現(xiàn)移動(dòng)的較大紅色弧點(diǎn),并伴隨大量細(xì)小的白色火花,此時(shí)才是MAO階段。繼續(xù)通電一段時(shí)間,紅色弧點(diǎn)逐漸變大,顏色逐漸變深,最終形成橘紅色的火花并伴有大量白色火花;隨反應(yīng)的繼續(xù)進(jìn)行,一些跳動(dòng)的弧點(diǎn)不再移動(dòng),而是停在某一部位連續(xù)放電,并發(fā)出尖銳的爆鳴聲,此為弧光放電階段,是一個(gè)擊穿破壞膜層的過程。若停止通電,紅色弧點(diǎn)減弱,數(shù)量逐漸減少,直至完全消失,即為熄弧階段。
由于MAO是將操作電壓由低壓Faraday區(qū)引入到高壓放電區(qū)域,整個(gè)過程涉及到化學(xué)、電化學(xué)、熱化學(xué)及等離子體化學(xué)的共同作用,其放電原理及膜層生長機(jī)制非常復(fù)雜。科學(xué)家根據(jù)火花放電的現(xiàn)象,提出了多種假設(shè)和模型解釋微弧放電機(jī)理。1967年,Wood等提出“電子雪崩”模型,認(rèn)為在較高電場的影響下,溶液中的電子或陰離子進(jìn)入氧化膜,與膜層中其他原子發(fā)生碰撞后,電離產(chǎn)生新的電子,膜層中電子電流密度隨之不斷增加并引起火花放電。1971年,Vijh的研究闡述了產(chǎn)生火花放電的原因,并利用“電子雪崩”模型對放電過程中的析氧反應(yīng)進(jìn)行了解釋。隨后不久,Ikonopisov[37]提出了電子“Schottky隧道”模型,用定量的理論模型推測了電子被注入到氧化膜導(dǎo)帶中的過程,以及引起火花放電的原因,從而解釋引起“雪崩”電子的來源。同時(shí),他首次引入了擊穿電位 (UB) 的概念,指出了影響UB的主要因素,包括基體金屬材料的性質(zhì)、所使用電解液的配方以及溶液的導(dǎo)電性能等。由于電流密度、電極的形狀以及升壓方式等對UB的影響較小,從而建立了電導(dǎo)率和UB與溶液溫度之間的函數(shù)關(guān)系。同時(shí),Van等進(jìn)一步研究了火花放電的整個(gè)過程,指出“電子雪崩”總是在氧化膜層最薄弱、最容易被擊穿的區(qū)域首先進(jìn)行,而放電時(shí)的巨大熱應(yīng)力則是產(chǎn)生“電子雪崩”的主要?jiǎng)恿ΑM辏琋ikoiaev等認(rèn)為,在氧化膜內(nèi)部存在大量的放電通道,在放電通道與阻擋層表面接近的區(qū)域內(nèi)產(chǎn)生放電現(xiàn)象,促進(jìn)膜層生長,從而提出了微橋放電模型。20世紀(jì)80年代中期,Albella等認(rèn)為進(jìn)入膜層中的電解質(zhì)是MAO放電過程的高能離子。在氧化過程中,電解質(zhì)離子形成雜質(zhì)放電中心,產(chǎn)生等離子體放電,使電解質(zhì)離子、氧離子與基體金屬材料形成強(qiáng)烈反應(yīng)而結(jié)合在一起;同時(shí)產(chǎn)生大量的熱被釋放出來,使已經(jīng)形成的膜層在基體金屬材料的表面熔融和燒結(jié)后便形成具有陶瓷結(jié)構(gòu)的MAO膜層。而且,他還進(jìn)一步完善了“Schottky隧道”模型,闡明了UB與電解質(zhì)濃度,膜層厚度與電壓之間的關(guān)系。Krysmann等認(rèn)為MAO能夠在各種形狀的零件上形成膜層的原因,是因?yàn)樵陉枠O材料表面附近形成了類陰極 (電解液/氣體界面),使得表面發(fā)生均勻極化的結(jié)果,從而揭示了膜層結(jié)構(gòu)與對應(yīng)電壓間的關(guān)系,并提出了火花沉積模型。在以上放電理論模型基礎(chǔ)上,Epelfeld等提出了“孔內(nèi)放電(discharge-in-pore)”模型,認(rèn)為氧化膜微孔底部絕緣層的介電擊穿,誘發(fā)微孔內(nèi)的氣體放電,從而產(chǎn)生微弧放電現(xiàn)象。隨后,Yerokhin等研究證實(shí)了微弧放電直徑非常接近MAO膜外層微孔的平均尺寸。而Hussein等和Wang等借助光發(fā)射光譜技術(shù)(OES)也表明了微孔內(nèi)存在氣體放電現(xiàn)象。“孔內(nèi)放電”模型定性地解釋了厚MAO膜在低壓條件也能穩(wěn)定生長的原因。最近,Mi等根據(jù)金屬和氣體電子特點(diǎn),提出了“熱電子散射(thermalelectron emission)”模型,分析認(rèn)為由于電子隧道效應(yīng)和雜質(zhì)離子化,在微弧放電前的絕緣層表面能夠產(chǎn)生電子電流,高能量電子電流引起熱電子散射,散射出的電子與氣泡內(nèi)的原子碰撞并使其離化,從而形成等離子體放電。這一理論模型與他自己的實(shí)驗(yàn)結(jié)果很好地吻合,但還有待進(jìn)一步的證實(shí)。
由此可見,MAO過程的非Faraday特性,以及伴隨的放電現(xiàn)象和復(fù)雜的化學(xué)過程,至今還未形成一套全面而合理的模型解釋放電現(xiàn)象。而關(guān)于膜層生長機(jī)理,在不同的電解液體系中存在差異,這在文獻(xiàn)中有詳細(xì)報(bào)道,這里不再贅述。
2 MAO應(yīng)用于鎂合金表面防護(hù)
2.1 電源特性
MAO處理高耗能是限制其廣泛應(yīng)用的主要瓶頸,而電源是MAO處理中可以靈活控制的系統(tǒng)環(huán)節(jié),改進(jìn)電源特性,優(yōu)化電源電參數(shù),是降低能耗并獲得最佳涂層性能的重要途徑。單一電源形成的MAO膜質(zhì)量和性能不佳,因而先后出現(xiàn)了直流電源、交流電源、單脈沖電源、直流和交流復(fù)合電源、直流和脈沖復(fù)合電源、雙脈沖電源、三角波電源等。Jin等分別采用直流和高頻雙極性脈沖電源對AZ91D鎂合金進(jìn)行MAO處理。結(jié)果表明,處理時(shí)間相同時(shí),雙極性脈沖電源處理的膜層生長速率快,膜層更致密,硬度高,耐磨性更好。Wang等研究也證實(shí)了雙極性模式獲得的膜層結(jié)構(gòu)致密,防腐性能更佳。Hussein等詳細(xì)研究了單極、雙極、單極+雙極和雙極+單極模式下的等離子體過程與膜層結(jié)構(gòu)的關(guān)系,結(jié)果表明采用單極+雙極的電源模式獲得的膜層孔隙率最低,膜層致密。
因此,從工藝開發(fā)需求和電源開發(fā)趨勢看,雙極性不對稱脈沖電源或混合電源將是電源發(fā)展的主流。
2.2 工作模式
不同電源均可通過恒流、恒壓或恒功率等工作模式實(shí)現(xiàn)MAO處理。一般來說,恒流控制便于計(jì)算和控制能耗,但MAO的后期容易破壞膜層;恒壓控制可以有效地解決恒流模式中電解液對基體鈍化性能差的問題,能方便控制膜層的厚度及表面均勻度,但對電源功率的要求較高,存在MAO后期擊穿不夠,導(dǎo)致所制得的膜層較薄。研究人員在7 g/L NaOH+4 g/L (NaPO3)6+0.4 g/L乙酸鈣體系中比較了AZ91D鎂合金在3種電源模式 (恒壓、恒流和恒功率) 下涂層的結(jié)構(gòu)及性能,結(jié)果見圖3。表明,在相同時(shí)間內(nèi),恒壓模式下的MAO膜具有最大的粗糙度、厚度和耐均勻腐蝕性能;而恒功率模式可獲得表面粗糙度最低、致密及最佳耐點(diǎn)腐蝕能力的膜層。在硅酸鹽體系中,本課題組的研究進(jìn)一步表明,與恒壓模式相比,恒功率控制使得鎂合金MAO初期在大電流的環(huán)境下起弧,而后期是在高電壓環(huán)境下完成MAO,整個(gè)過程都是在較為極端的條件下進(jìn)行,不容易控制,導(dǎo)致所形成的MAO膜具有較少的微孔,但較大的孔徑和較快的生長速度,不利于提高膜層的防腐性能。
2.3 電參數(shù)
MAO電參數(shù)主要包括電流密度 (恒流模式)、氧化電壓 (恒壓模式)、頻率 (脈沖電源) 和占空比 (脈沖電源) 等。不同電源類型或工作模式,各電參數(shù)對膜層厚度、表面結(jié)構(gòu)及性能的影響規(guī)律基本一致。但由于電解液類型的不同,各參數(shù)的最佳工藝存在差異。
2.3.1 電壓
在恒壓模式下,隨電壓的升高,氧化膜生長速率增大,膜層厚度、表面孔隙率及防腐性均增加,但電壓過高,易導(dǎo)致膜層局部擊穿及防腐性能失效。在恒流模式下,存在起始電壓與終止電壓。Zhang等研究表明,工藝參數(shù)對耐蝕性影響程度從高到低的順序?yàn)椋航K止電壓>頻率>占空比>電流密度。試樣表面粗糙度隨終止電壓的升高而增加,與起始電壓變化的關(guān)系不明顯。當(dāng)起始電壓相等時(shí),終止電壓愈大,膜層越厚,但孔徑增大,顯微缺陷增多,耐蝕性下降。當(dāng)終止電壓相等時(shí),起始電壓愈高,膜層厚度也愈厚。
有研究表明,在恒壓模式下施加負(fù)向電壓,能中和絕緣膜層上的電荷積累,有利于膜層表面低溫相和表面疏松物質(zhì)的溶解,制備更致密的膜層,從而提高膜層的防腐性能。
董海榮等在硅酸鹽電解液體系中采用恒壓、變壓兩種加壓方式研究AZ91D鎂合金MAO膜層的厚度、表面形貌、物相組成及防腐性隨時(shí)間的變化規(guī)律。結(jié)果表明,兩種加壓方式下,膜層結(jié)構(gòu)隨時(shí)間的變化規(guī)律基本相同,恒壓加壓方式下膜層的耐蝕性不斷增強(qiáng),變壓加壓方式下則先增大后減小;與變壓加壓方式相比,恒壓加壓方式下膜層生長前期的生長速率較大,更有利于工業(yè)化生產(chǎn)。
呂維玲等在恒壓模式硅酸鹽體系中研究了加壓幅度和加壓時(shí)間間隔對MAO膜層結(jié)構(gòu)和性能的影響。結(jié)果表明,隨著加壓幅度和加壓時(shí)間間隔的增大,膜層的厚度、孔隙率和結(jié)合力都呈先增大后減小的趨勢;在加壓幅度為25 V、加壓時(shí)間間隔為150 s時(shí),所獲得的MAO膜層防腐性能最佳。
可見,采用不同的加壓方式、加壓幅度以及負(fù)向電壓等工藝,為恒壓模式電參數(shù)工藝優(yōu)化提高M(jìn)AO膜防腐性能提供了有效途徑。
2.3.2 電流密度
在恒流控制模式下,電流密度是決定氧化過程能否進(jìn)行的重要指標(biāo),是影響膜層性能和質(zhì)量的決定性因素。研究表明,隨著電流密度的增大,微弧放電能量增大,熔融物增多,放電微孔孔徑增大,氧化膜層生長速率增大,膜層厚度隨之增加,粗糙度增大,晶化程度增大。防腐性能和硬度隨電流密度升高而增大。但超過極限值時(shí),膜層生長速率下降,致密性變差,防腐性能降低。依據(jù)文獻(xiàn)數(shù)據(jù),電流密度參數(shù)主要集中在0.2~20 A/dm2 之間。
2.3.3 頻率 頻率是指單位時(shí)間脈沖震蕩的次數(shù)。無論是恒壓模式或恒流模式,作用在膜層上的能量相差不大,電場的驅(qū)動(dòng)力也近似相同,膜層生長速率基本不變,因此對膜層厚度的變化影響較小。但隨頻率的升高,單位時(shí)間脈沖震蕩的次數(shù)增加,單位時(shí)間發(fā)生擊穿區(qū)域的數(shù)量增多,單脈沖能量也就越小,發(fā)生一次擊穿時(shí)能量也小,膜層表面放電微孔孔徑較小,膜層較致密,耐蝕性較好。最近,蘇立武等研究得到了相反的結(jié)果。如圖4所示,在脈寬和脈沖電流不變的條件下,隨著脈沖頻率增加膜層表面火山堆狀微孔數(shù)量減少,孔徑增大。分析認(rèn)為,脈沖頻率的增加并不影響單脈沖能量,而是增加了單位時(shí)間內(nèi)試樣表面的總能量,導(dǎo)致多次重復(fù)擊穿的熔融產(chǎn)物數(shù)量增多,所需放電通道直徑變大。關(guān)于該實(shí)驗(yàn)結(jié)果及該作用下膜層的防腐性是否提高,還有待于進(jìn)一步證實(shí)。
2.3.4 占空比
占空比是在一個(gè)脈沖周期內(nèi)電流導(dǎo)通時(shí)間與整個(gè)周期的比值,它決定了單脈沖的放電時(shí)間。研究表明,占空比低于45%時(shí),對膜層的防腐性能影響不大。但高于此值時(shí),膜層孔徑增大,表面出現(xiàn)擊穿破壞,從而導(dǎo)致防腐性能降低。這是由于占空比越大,導(dǎo)致單脈沖放電時(shí)間越長,樣品表面能量過大,會使膜層局部發(fā)生強(qiáng)烈放電,引起膜層表面燒損;同時(shí),表面能量增加導(dǎo)致熱析出增大,放電區(qū)的溫度迅速升高,在放電區(qū)膜層的熔融量增多,熔融物在快速凝固時(shí)形成較大氣孔,從而導(dǎo)致其致密性下降,防腐性能降低。孫磊等[71]研究了恒流模式下階段占空比對膜層結(jié)構(gòu)和性能的影響,分析認(rèn)為MAO初期應(yīng)采用較大占空比有利于鈍化膜擊穿,MAO中期適當(dāng)降低占空比有利于膜層平穩(wěn)生長,膜層生長后期采用較小占空比可以較好地修復(fù)膜層,從而可獲得微觀結(jié)構(gòu)均勻致密的耐蝕膜層。
2.4 電解液
MAO電解液的主要作用有:作為電流傳導(dǎo)的介質(zhì);以含氧鹽的形式提供所需要的氧;電解質(zhì)的組分通過電化學(xué)反應(yīng)進(jìn)入膜層,改善MAO膜性能。一般來說,電解液由成膜劑和添加劑兩類物質(zhì)組成。成膜劑往往是Mg的鈍化劑,由氟化物、氫氧化物、碳酸鹽、硼酸鹽、磷酸鹽、硅酸鹽和鋁酸鹽等物質(zhì)中的一種或幾種組成,它們能與Mg2+形成穩(wěn)定沉淀,是陽極氧化膜的主要成分。添加劑是以改變工藝參數(shù)或改善膜層性能為目的而添加的物質(zhì),如醇、羧酸和有機(jī)胺可以降低電流密度或起弧電壓,Al2O3,SiO2和ZrO2等納米顆粒可以增強(qiáng)膜層耐磨性能。
2.4.1 常用電解液及影響因素
目前,常用電解液主要有硅酸鹽體系、磷酸鹽體系、鋁酸鹽體系以及它們之間的混合體系。但磷酸鹽電解液污染環(huán)境,而鋁酸鹽、硅酸鹽體系更易成膜,制備的膜層防腐性能較好。Chai等分別研究了以Na2SiO3,Na3PO4,NaAlO2和Na2MoO4為成膜劑的電解液體系,認(rèn)為硅酸鹽體系得到的膜層耐蝕性最佳。隨后,Ghasemi等[74]的研究也證實(shí)了在KOH與Na2SiO3,Na3PO4和NaAlO2中任意單一組合電解液中,膜層對MAO處理液中的離子吸附具有選擇性,吸附性最強(qiáng)的是SiO32-,且在硅酸鹽體系中獲得的膜層最厚,并具有最小的孔密度和最佳的耐蝕性能。然而,Seyfoori等研究表明,AZ31鎂合金在磷酸鹽體系中獲得的MAO膜比硅酸鹽體系中的更厚、更耐蝕。Bai等比較了AZ91D鎂合金在磷酸鹽體系、硅酸鹽體系及磷酸-硅酸鹽體系電解液中表面MAO膜層的性能,結(jié)果表明,在0.1 mol/L的磷酸鹽體系中引入0.08 mol/L的Na2SiO3時(shí),便使電解液的起弧電壓從磷酸鹽體系的400 V降到了200 V,且膜層孔隙率降低,微孔直徑減小,耐蝕性增強(qiáng)。Mori等研究了磷酸鹽與硅酸鹽濃度比 (100∶0~0∶100) 對MAO膜結(jié)構(gòu)和性能的影響,結(jié)果表明,當(dāng)磷酸鹽與硅酸鹽濃度比為20% (即P∶Si=20∶80) 時(shí),在AZ31B鎂合金表面獲得的MAO膜具有最佳的腐蝕防護(hù)能力。因此,以硅酸鹽為主的復(fù)合電解液已成為當(dāng)前研究的主要體系。
電解液的電導(dǎo)率及電解質(zhì)濃度一直被認(rèn)為是MAO過程中影響起弧電壓的關(guān)鍵因素,也決定著膜層的結(jié)構(gòu)和性能。研究認(rèn)為,硅酸鹽體系以及硅酸鹽-磷酸鹽復(fù)合體系溶液的電導(dǎo)率為4~6 (Ω。m)-1時(shí),所得膜層的防腐性能最佳。張龍等[80]的研究認(rèn)為電解質(zhì)濃度,尤其是主鹽如硅酸鈉,顯著影響鎂合金微弧等離子體的誘發(fā)過程和膜層的微觀結(jié)構(gòu)。分析也表明溶質(zhì)離子種類才是誘發(fā)微弧等離子體和促進(jìn)膜層生長的最主要因素,pH值和電導(dǎo)率并不是本質(zhì)因素。姚力夫等研究表明,電解質(zhì)濃度影響MAO膜的厚度、表面結(jié)構(gòu)及性能,在硅酸鹽電解液中引入5 g/L (NaPO3)6時(shí)在鎂合金表面獲得的膜層耐蝕性最佳。Simchen等證實(shí)MAO的起弧電壓取決于電解液中陰離子的類型及濃度,而不是電解液電導(dǎo)率,這與文獻(xiàn)的研究結(jié)果一致。Ono等也進(jìn)一步證實(shí)相同電參數(shù)條件下,MAO膜的厚度和耐蝕性取決于電解質(zhì)濃度,而與電流密度無關(guān)。可見,電解質(zhì)的濃度過低,MAO過程難以進(jìn)行;電解質(zhì)的濃度過高會加速氧化膜的溶解,且影響膜層的致密性和防腐性能,必須控制在一個(gè)合適的范圍內(nèi)。
除了電解質(zhì)種類、濃度及其溶液電導(dǎo)率外,電解液溫度和pH值也會影響MAO過程的成膜速率和膜層質(zhì)量。電解液溫度對溶液電導(dǎo)率的影響較大,溫度每升高10 ℃,電解液電導(dǎo)率約增加12%。而電導(dǎo)率的增加會減小膜層的起弧電壓,促進(jìn)膜層生長,增大表面微孔尺寸,容易降低膜層防腐性能。此外,過高的溫度還會造成膜層表面過燒現(xiàn)象。但過低的溫度,MAO膜的生長速率慢,性能較差。因此,電解液溫度通常控制在20~40 ℃之間,尤以約30 ℃獲得的膜層性能最佳。對于鎂合金MAO電解液的pH值一般控制在10~12之間,過高的pH值會加速膜層的溶解,降低膜層的致密性。此外,過高的pH值,容易縮短電解液的使用壽命,增加MAO處理成本。
2.4.2 添加劑
電解液添加劑可以分為有機(jī)添加劑和無機(jī)添加劑兩大類。有機(jī)添加劑如醇類、有機(jī)胺類、有機(jī)硅氧烷、有機(jī)酸類及它們的鹽等物質(zhì),這類添加劑主要是在MAO過程中起到抑弧作用,從而獲得表面微孔分布均勻的氧化膜,提高膜層的致密性和防腐性;同時(shí)可起到降低能耗的效果,見表1。無機(jī)添加劑如石墨烯、Al2O3、SiO2等物質(zhì),這類添加劑在MAO過程中可以參與成膜,從而提高膜層的防腐、抗磨等性能,見表2。關(guān)于添加劑的種類和作用,在文獻(xiàn)中都有詳細(xì)分析,這里僅列表比較部分添加劑的作用,以供參考,不再詳細(xì)贅述。
2.5 后處理
由于微弧放電作用導(dǎo)致MAO膜具有微觀多孔的結(jié)構(gòu),這種結(jié)構(gòu)特征大大降低了膜層對基體的防腐抗磨性能。因此,必須對MAO膜進(jìn)行封孔或復(fù)合涂層處理來提高其對鎂合金基體腐蝕磨損的防護(hù)能力。
2.5.1 封孔處理
封孔的主要方法有沸水、鉻酸鹽、硅酸鹽、磷酸鹽、碳酸鹽、溶膠-凝膠、石蠟以及有機(jī)物封孔等。蔣百靈等對MAO膜用石蠟、丙烯酸和沸水溶液進(jìn)行封孔處理,分析表明,石蠟封孔耐蝕性效果最好。Kim等比較了NaOH和Al(OH)3溶液對AZ91鎂合金MAO膜封孔的耐蝕性能,研究表明,1 mol/L NaOH在373 K處理30 min的封孔效果最佳。但袁兵等對MAO樣品分別進(jìn)行浸石蠟、噴涂聚苯乙烯泡沫銀粉漆、電泳處理,經(jīng)研究表明,MAO膜與電泳漆結(jié)合膜層的耐蝕性最佳。Jiang等、Zhang等以及本課題組利用MAO技術(shù)在鎂合金表面構(gòu)筑微納結(jié)構(gòu),然后進(jìn)行疏水改性,有效地提高了鎂合金的耐蝕性能。圖5為MAO膜改性前后的表面形貌及其表面接觸角,改性后涂層表面表現(xiàn)出超疏水性能。Cui等利用聚甲基三甲氧基硅烷封孔MAO處理的AZ31鎂合金,在表面獲得了自愈合MAO/聚硅烷復(fù)合涂層,有效提高了MAO膜的長效腐蝕防護(hù)能力。陳寧寧等將石墨烯與硬脂酸共混溶液滴涂在MAO處理的AZ91鎂合金表面,獲得靜態(tài)接觸角達(dá)到162°的超疏水膜層,有效地提高了MAO膜對基體的腐蝕防護(hù)能力。然而,這些封孔及表面疏水改性,主要依靠物理吸附作用,效果持久性和耐磨性能較差。
最近,環(huán)境友好的鈰鹽封孔處理引起了很多學(xué)者的注意。Mohedano等研究了鈰鹽濃度和封孔時(shí)間對MAO膜層防護(hù)性能的影響。結(jié)果表明,MAO處理的AM50鎂合金在10g/LC(NO3)3.6H2O+0.3 g/L H2O2溶液中30 ℃封孔3 h,獲得的膜層封孔效果最佳。如圖6所示,封孔過程中產(chǎn)生的CeO2進(jìn)入了氧化膜微孔內(nèi),從而提高了膜層的致密性,進(jìn)一步提高了膜層的腐蝕防護(hù)能力。隨后,Van Phuong等[156]采用兩次封孔工藝密封MAO處理的AZ31鎂合金樣品。首先在0.023 mol/L Ce(NO3)3.6H2O+0.25 mol/L H2O2溶液中 (25±1) ℃封孔20 min,然后在0.1 mol/L NaH2PO4溶液中 (90±1) ℃封孔20 min。結(jié)果顯示,單一封孔處理的樣品在0.5 mol/L NaCl溶液中浸泡僅5 d便出現(xiàn)明顯的腐蝕特征,而復(fù)合封孔處理的樣品浸泡20 d未見腐蝕現(xiàn)象。
韓恩厚團(tuán)隊(duì)利用電解液中金屬復(fù)鹽在高溫時(shí)發(fā)生分解參與成膜的原理,先后開展了氟鋯酸鹽、氟鈦酸鹽自封孔MAO技術(shù)。如圖7所示,MAO膜表面微孔內(nèi)填充了物質(zhì),封住了微孔。隨后,本課題組通過在硅酸鹽體系中引入K2ZrF6,也獲得了自封孔的MAO膜。這種自封孔MAO樣品的耐蝕性比普通微弧氧化膜高,表面無需涂覆有機(jī)涂層就可以為Mg基體提供良好的腐蝕防護(hù)。
此外,陳宏等利用外加電場作用下膠體粒子向工件表面移動(dòng)的原理,提出外加電場和MAO相結(jié)合的方法獲得了自封孔MAO膜。如圖8所示,通過外加電場驅(qū)動(dòng)帶負(fù)電的Zr(OH)4膠體粒子進(jìn)入微孔實(shí)現(xiàn)了微孔封閉的MAO膜。研究也表明,這種自封孔MAO膜樣品的耐蝕性與膜層孔隙率及封孔填充物的成分和形態(tài)具有極大的相關(guān)性,且可通過調(diào)整外加電場強(qiáng)度和時(shí)間實(shí)現(xiàn)對自封孔的調(diào)控,從而改善防腐性能。Rehman等研究了兩步MAO處理AZ91D鎂合金工藝。研究表明,第一步在Na2SiO3體系中氧化15min,然后在含有K2ZrF6的硅酸鹽復(fù)合體系中氧化10 min時(shí),涂層樣品具有優(yōu)異的耐蝕性能。如圖9所示,分析認(rèn)為第二步MAO優(yōu)先在第一步MAO膜的微孔區(qū)域發(fā)生擊穿放電,從而實(shí)現(xiàn)對一次MAO膜的封孔,涂層致密化(表面孔隙率從5.6%降至1.2%),進(jìn)一步提高了膜層的硬度和防腐性能。
由此可見,通過電解液摻雜,或外加電場,或多次工藝復(fù)合,都可實(shí)現(xiàn)封孔MAO膜。但相關(guān)的形成機(jī)理、優(yōu)化工藝及性能強(qiáng)化仍需深入研究。
2.5.2 復(fù)合涂層處理
基于MAO膜與鎂合金基體呈冶金結(jié)合及其表面微觀多孔的特性,將物理氣相沉積、有機(jī)涂層、大氣等離子噴涂、化學(xué)鍍/電鍍等技術(shù)與MAO復(fù)合,可制備性能優(yōu)異的功能涂層。如近期開展的工作:Yang等在鎂合金表面構(gòu)筑MAO/(Ti:N)-DLC耐磨涂層;本課題組在鎂合金表面構(gòu)筑硬質(zhì)涂層;Fan等在MB26鎂合金表面制備MAO/(APS)Yb2SiO5熱障涂層。這些復(fù)合涂層處理大大提高了MAO膜對鎂合金基體的防腐抗磨性能。有關(guān)這方面的工作,在文獻(xiàn)中有詳細(xì)綜述,這里不再贅述。
2.6前處理
MAO處理前,對材料表面進(jìn)行適當(dāng)?shù)那疤幚韥砀淖兤浔砻娴慕M織結(jié)構(gòu),對后續(xù)的MAO處理及膜層的性能影響也是非常重要的。Wang等通過含有Al(NO3)3的溶液對AZ91D鎂合金進(jìn)行超聲預(yù)處理,結(jié)果提高了MAO膜均勻性,增強(qiáng)了膜層的腐蝕防護(hù)能力。Krishna等首次采用冷噴涂技術(shù)在AZ91鎂合金表面預(yù)沉積Al層,然后對其進(jìn)行MAO處理,結(jié)果獲得了梯度成分分布的鎂鋁尖晶石結(jié)構(gòu)涂層,表現(xiàn)出了良好的防腐性能。Cai等首先對AZ91D鎂合金進(jìn)行硝酸鈰化學(xué)轉(zhuǎn)化處理,然后進(jìn)行MAO處理,獲得了CeO2摻雜的致密MAO膜,并表現(xiàn)出優(yōu)異的耐蝕性能。Hariprasad等比較了鈰鹽轉(zhuǎn)化作為MAO前處理和后處理對膜層防腐性能的影響。分析表明,鈰鹽轉(zhuǎn)化膜前處理能夠提供均勻的表面結(jié)構(gòu),進(jìn)一步增強(qiáng)了后續(xù)MAO膜的致密性,從而提高了其對基體的腐蝕防護(hù)能力。可見,基體表面微結(jié)構(gòu)或表面狀態(tài)對MAO膜性能有顯著的強(qiáng)化作用。
宋東福等研究表明,基體表面粗糙度影響MAO過程及膜層的防腐性能,與表面噴砂 (Ra 2.2 μm) 相比,砂紙打磨 (Ra 0.5 μm) 樣品的耐蝕性能提高了40%。Gheytani等[174]利用表面機(jī)械研磨技術(shù)(SMAT)實(shí)現(xiàn)AZ31B鎂合金表面納米化(5~10 nm),再經(jīng)MAO處理所得膜層樣品的極化電阻增加了700%,耐磨性增加了105%。由于表面機(jī)械研磨需要在真空環(huán)境中進(jìn)行,限制了樣品尺寸,加之環(huán)境粉塵和噪音污染,不利于大規(guī)模應(yīng)用。Chen等[175]采用表面超聲冷鍛工藝 (UCFT) 對鎂合金進(jìn)行表面納米化 (48.67 nm),分析結(jié)果也證實(shí)表面納米化細(xì)化了AZ31B鎂合金表面晶粒,降低了表面粗糙度,獲得了致密耐蝕的MAO膜。可見基體表面晶粒細(xì)化影響MAO膜層的致密性。
Wang等通過激光表面熔融技術(shù)對AZ91D鎂合金進(jìn)行預(yù)處理,然后再進(jìn)行MAO處理。研究表明激光表面熔融處理促進(jìn)了鎂合金表面晶粒細(xì)化、Al富集以及第二相粒子(Mg17Al12)的重新分布,增加了MAO膜層的致密性,顯著提高了復(fù)合膜層的耐蝕性能。Wei等研究了Al含量對MAO膜結(jié)構(gòu)及性能的影響。結(jié)果表明,隨著Al含量增加,鎂合金中β相和共晶(α+β)相數(shù)量增多,膜層孔隙率先減小后增加,從而影響了膜層的耐蝕性。隨后,該課題組的Chen等證實(shí)了第二相粒子的尺寸影響MAO膜的結(jié)構(gòu)。尺寸越細(xì)小,分布越均勻,所得膜層就越致密,耐蝕性就越好。
此外,基體表面微觀結(jié)構(gòu)構(gòu)筑,如微米凹槽,對MAO能耗、膜層生長速率、硬度及耐蝕性能影響較大,但在鎂合金表面報(bào)道較少,有待于進(jìn)一步開展相關(guān)研究。
3 存在的問題與建議
從國內(nèi)第一篇鎂合金表面微弧氧化文獻(xiàn)報(bào)道至今,經(jīng)過二十多年的研究,鎂合金表面MAO處理技術(shù)已經(jīng)有了長足的發(fā)展,但MAO技術(shù)及其在鎂合金表面的理論研究和應(yīng)用仍存在許多不足,亟待進(jìn)一步完善。
(1)MAO機(jī)理:仍無法用清晰的理論模型闡明MAO的火花放電及成膜過程,亟待從熱力學(xué)、動(dòng)力學(xué)角度及現(xiàn)代高科技分析技術(shù),深入分析并完善理論模型,用于指導(dǎo)微弧氧化。
(2)鎂合金基體:基體的元素組成及表面狀態(tài),顯著影響MAO膜的形成過程及性能,但由于鎂合金基體組成的多元化、MAO前處理的多途徑及研究的分散性,缺乏對某一合金MAO前處理的系統(tǒng)性研究。
(3)MAO電源:電源決定著不同工作模式下各電參數(shù)的特性,但各研究機(jī)構(gòu)采用的電源或是企業(yè)成熟的設(shè)備技術(shù)或是自己研發(fā)的設(shè)備,加之在部分文獻(xiàn)中對電源設(shè)備的各參數(shù)描述不夠詳細(xì),導(dǎo)致各文獻(xiàn)之間所得膜層與影響因素的關(guān)聯(lián)性存在差異,數(shù)據(jù)的有效性和可參考性不足。
(4) 電解液:電解質(zhì)種類及濃度顯著影響MAO過程的起弧電壓與膜層性能,但不同電源電參數(shù)調(diào)控下的電解液組成及電解質(zhì)濃度差異較大,各組成尤其是陰離子對膜層某一性能 (如防腐性) 的有益貢獻(xiàn)和作用機(jī)理不清楚,加之文獻(xiàn)中所采用的濃度單位或是g/L,或是mol/L,導(dǎo)致部分優(yōu)化配方對理論研究或大規(guī)模工業(yè)化應(yīng)用的可參考性不足。
(5) MAO膜性能強(qiáng)化:為強(qiáng)化MAO膜性能,可通過電解液摻雜、多步MAO處理、MAO輔助、MAO膜封孔及復(fù)合涂層等技術(shù)實(shí)現(xiàn),但這些強(qiáng)化技術(shù)之間相對獨(dú)立,對MAO膜性能的強(qiáng)化程度缺乏比較,且在機(jī)理、工藝優(yōu)化及性能關(guān)聯(lián)性等方面的研究不夠完善。
此外,也期望國內(nèi)知名機(jī)構(gòu)或?qū)W者,建立MAO處理技術(shù)相關(guān)數(shù)據(jù)庫,實(shí)現(xiàn)各電源、MAO工藝之間的數(shù)據(jù)共享,提高各數(shù)據(jù)的有效性和參考性,促進(jìn)MAO技術(shù)的研究及其在工業(yè)中的大規(guī)模應(yīng)用。
免責(zé)聲明:本網(wǎng)站所轉(zhuǎn)載的文字、圖片與視頻資料版權(quán)歸原創(chuàng)作者所有,如果涉及侵權(quán),請第一時(shí)間聯(lián)系本網(wǎng)刪除。
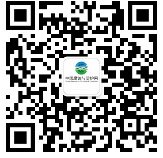
官方微信
《中國腐蝕與防護(hù)網(wǎng)電子期刊》征訂啟事
- 投稿聯(lián)系:編輯部
- 電話:010-62313558-806
- 郵箱:fsfhzy666@163.com
- 中國腐蝕與防護(hù)網(wǎng)官方QQ群:140808414