導讀: 在韌性斷裂界,最令人困惑的爭議之一是在剪切主導加載過程中,預測的應變-破壞值與實驗觀察到的應變-破壞值之間存在很大差異。目前提出的解決方案側重于更好地解釋偏應力狀態如何影響空洞生長,或者側重于在微觀尺度而不是宏觀尺度上測量應變。雖然這些方法是有用的,但它們并沒有解決問題的一個重要方面:通常考慮的唯一斷裂微機制是空洞成核、生長和聚并(對于拉伸主導加載),以及剪切局部化和空洞聚并(對于剪切主導加載)。因此,當前的現象學模型側重于基于材料的應力狀態和應變硬化能力來預測這些機制之間的競爭。通過對銅、鎳和鋁這三種具有中高層錯能的高純度面心立方(FCC)金屬的斷裂過程進行表征,解決了這些問題。對于給定的應力狀態和材料,幾種機制經常以順序的方式共同作用,導致斷裂。破壞機制的選擇在很大程度上受到撕裂開始前發生的塑性誘導的微觀結構演變的影響,這可能會產生或消除空隙成核的場所。在宏觀尺度上,觀察到不涉及破裂或孔隙生長的破壞機制有助于隨后的孔隙生長和聚并過程。雖然本研究的重點是純金屬的損傷積累,但這些結果也適用于理解工程合金的失效。
隨著20世紀斷裂力學的出現,許多斷裂問題變得相對容易預測。目前,基于線彈性斷裂力學和彈塑性斷裂力學的概念被廣泛用于預測韌性金屬的破壞。此外,許多基本問題,如拉伸和剪切主導載荷之間延性的相對差異,仍然沒有答案。在這種情況下,本研究的目的是研究韌性斷裂的機制和控制它們的因素。
在目前的研究中,我們提出骨折通常是由多種機制的順序發展控制的。此外,我們假設這些機制不僅相互競爭,而且可以相互促進。一個經典的,但經常被忽視的例子是結構金屬的杯錐破壞。大多數拉伸桿的斷口表面既表現為中心平坦的“纖維”韌性韌窩區,又表現為向外圍剪切唇區明顯的過渡。
為了驗證這些假設,Philip J. Noell團隊采用中斷變形實驗和各種表征方法表征了高純銅、鎳和鋁的斷裂過程。這三種材料都是面心立方(FCC),在準靜態、室溫變形時通過滑移變形,表明并非所有FCC金屬失效的機制相同。選擇了兩種應變硬化能力截然不同的材料(銅和鎳)。選取高純鋁,研究動態再結晶對斷裂過程的影響。在純度為99.99%或更高的樣品的室溫變形過程中,該材料觀察到動態再結晶[60e62]。本研究的重點是這三種材料的片材試樣在單軸拉伸下的破壞,但也對每種材料的絲材試樣的斷口表面進行了表征,以了解各向同性約束狀態下的損傷進展。
雖然這項研究僅限于高純度金屬,但這些結果也與含有第二相顆粒的金屬有關。在純金屬中,空洞在晶界和變形引起的位錯界等部位成核,而在大多數工程材料中,第二相顆粒是主要的空洞成核部位。第二相顆粒可能會加速空洞成核過程,并且在許多材料中都支持基于空洞的破壞機制。因此,純金屬的破壞過程比在大多數工程材料中觀察到的更廣泛的破壞機制,同時提供了關于基于空洞的破壞機制之間競爭的信息。
相關研究成果以“The mechanisms of ductile rupture”發表在Acta Materialia上
鏈接:https://doi.org/10.1016/j.actamat.2018.09.006
圖1(A)給出了Al 2024-T351試樣在不同應力三軸性(σm/σe)下的斷裂應變圖。
(b)中的圖像顯示了矩形Ti-6Al-4V試樣的拉伸斷裂面示例,該試樣在第二次Sandia斷裂挑戰中進行了單軸拉伸測試。在許多大塊金屬中,有兩種明顯而典型的機制:一個扁平的纖維帶,通常與空洞成核、生長和聚并有關,另一個是外圍剪切唇。
在應力三軸性約為1/3時,他們觀察到破壞應變隨著應力三軸性的減小而減小,在純剪切條件下達到最小值(應力三軸性為0),在負應力三軸性下迅速增加。這種關系如圖1 (a)所示。隨后的幾項研究報道了破壞應變與應力三軸性之間的類似關系[17e19]。因此,建立了剪切修正的Gurson、Mohr-Coulomb和其他[13,23e26]模型來捕捉剪切主導荷載的影響
圖2 7種不同宏觀韌性斷裂機制的示意圖如下:(a)空隙縮縮,(b)空隙剪切,(c)空隙片狀,
(d) Orowan交替滑移(OAS)機制,(e)縮縮至某一點導致試樣分離,
(f)和(g)分別顯示了單平面和多平面突變剪切導致試樣分離。文中提供了每種機制的詳細定義。
圖3給出了由(a)空隙縮縮、(b)空隙剪切、(c)空隙片化、(d) OAS機制、(e)縮縮至某一點、
(f)單平面突變剪切和(g)多平面突變剪切控制試樣的斷裂過程的SEM圖像。
表1提供了本研究測試材料的參考列表。對于每種材料,列出了線徑或片厚,以及與之相關的數字。如果在材料中觀察到夾雜物,則報告這些夾雜物的平均直徑。描述了七種不同的材料:一種鋁線材料、兩種鋁片材料、一種銅線材料、一種銅片材料、一種鎳線材料和一種鎳片材料。
圖4工程應力與工程應變數據表明,5N-Al、3N-Cu和4N-Ni片材的流動行為存在顯著差異。原理圖顯示了板材拉伸試樣的方向。這些工程應變數據是用立體DIC測量的。在3N-Cu拉伸試樣的圖像上顯示了一個示例DIC數據集。在這種情況下,當流動應力降至極限拉應力(UTS)的30%時,拉伸變形被中斷。
在0.127 mm/s的恒定位移速率下,采用位移控制對板材拉伸試樣進行試驗。圖4給出了3N-Cu、4N-Ni和5N-Al片材拉伸試驗的典型工程應力與工程應變數據。應變測量采用立體數字圖像相關(DIC),使用子集尺寸為35像素,步長為9像素,長度為2.35 mm的數字應變片。根據零負荷基線實驗,DIC延伸計測量噪聲水平為±0.004%。用于這些應變測量的延伸計如圖4所示,其中包含3N-Cu拉伸試樣的DIC數據。該圖還顯示了板材拉伸試樣的三個主軸:拉伸方向(TD)、長橫向(LTD)和短橫向(STD)。在所有情況下,STD都平行于原始薄片的厚度方向。
表2提供了對5N-Al、3NCu和4N-Ni片材進行的中斷拉伸試驗摘要。兩個5N-Al板材材料的拉伸試樣在10%的UTS處中斷。
表3總結了每種材料在損傷積累過程中控制斷裂的機制和相應的應力三軸性。OAS機制是指通過交替滑移過程形成空腔;通過OAS機制未觀察到孔洞成核。高局部應力三軸性定義為1/3(單軸拉力)或更大,例如,在剪切帶形成之前頸規區域的應力狀態。低局部應力三軸性定義為介于0到1/3之間(剪切和拉伸混合),例如在剪切帶形成后頸規區域的應力狀態。
圖5(a)鋁、(b)銅、(c)鎳三種高純度導線的斷口表面。
對于每種材料,提供以下(從左到右):斷裂面橫截面的電子通道對比(ECC)圖像,斷裂面的二次電子圖像(與斷裂面垂直),以及斷裂面的說明性草圖。這些圖像突出了這三種金屬絲材料斷口表面的顯著差異。
圖6給出了兩種不同高純鋁材料的斷裂過程。
如圖(a)和(c)所示,多晶5N-Al材料因間隙頸縮而失效。
如圖(b)所示,動態再結晶(DRX)在5N-Al片材中產生了新的無應變晶粒。
如圖(d)和(e)所示,低晶4N-Al材料因縮頸到一點而失效。
圖7 3N-Cu薄片材料的斷裂過程用六個不同試樣的中間截面圖像來說明,
這些試樣在(a) 60%, (b) 55%, (c) 50%, (d) 40%, (e) 30%和(f) 5%的UTS處中斷。
覆蓋在每張圖像上的草圖突出了斷裂過程中此時的主要斷裂機制:
(a)擴散頸中的間隙頸縮導致的空洞成核和生長,(b)剪切帶中空洞片形成的新空洞成核,
(c)到(e)空洞片形成的空洞合并,以及(f) OAS機制導致該材料的最終斷裂。
圖8提供了圖7(c)所示的腔體的高倍圖像。作為參考,在圖7(c)中標記了(a)和(b)所示的區域。(a)中的圖像突出顯示了合并形成空腔的空腔兩側的拉伸空洞。
(b)中的二次電子圖像是在樣品的STD傾斜后拍攝的,顯示這些拉伸空洞通過空洞片聚集在一起。這可以從空腔兩側的一排排剪切凹陷中得到證明。
圖9破裂的3N-Cu薄片試樣的宏觀斷口圖如圖(A)所示。
(b)和(c)中的圖像是(A)中突出顯示的區域的高倍圖像。
這些圖像顯示,斷裂表面的中心覆蓋著拉伸韌窩,韌帶覆蓋著剪切韌窩。然而,該斷口的傾斜邊緣基本上是無韌窩的,這表明中心空腔是由OAS機制形成的。
圖10 4N-Ni片材的斷裂過程使用四個不同試樣的中間截面圖像來說明,
這些試樣在(a) 50%, (b) 25%, (c) 20%和(d) 10%的UTS處中斷。
疊加在每張圖像上的草圖突出了斷裂過程中此時的主要斷裂機制:
(a)宏觀剪切帶的形成,
(b)材料的兩半相互剪切,通過與(a)中的圖像進行比較可以看到,剪切帶中空洞的成核,隨后這些小空洞聚并導致(c)通過間隙剪切形成中心空洞,
(d)通過OAS機制形成該空洞。從這些圖像來看,從單面突變剪切到間隙剪切的轉變似乎是突然發生的,盡管突變剪切過程可能是通過沿剪切軸延長空洞而使空洞合并的。
圖11提供了如圖10(c)所示的空腔內部的二次電子圖像。這些圖像是在標本傾斜STD后拍攝的,以便對腔體內部進行成像。這些圖像突出顯示了空洞邊緣的部分,這些部分要么被剪切凹陷覆蓋,要么沒有凹陷。
圖12(A)是4N-Ni片試樣破裂的宏觀斷口圖。
(b)和(c)中的圖像是(A)中高亮顯示區域的高倍圖像。
這些圖像顯示,斷口表面的中心覆蓋著近似平行的韌窩,而邊緣基本上沒有韌窩。
圖13給出了鎳和銅的空隙體積分數(VNv)與von Mises應力(s)的關系圖。
由于銅具有比鎳大得多的應變硬化能力,對于給定的von Mises應力,銅中空隙間剪切所需的空隙體積分數明顯大于鎳。
圖14給出了斷裂機理圖的兩個概念性例子。
(a)中的圖大致基于在4N-Ni材料中觀察到的破壞順序,4N-Ni材料具有高的空穴成核阻力和低的空穴生長阻力。
(b)中的圖顯示了材料失效過程的一個例子,其中空洞成核幾乎完全被抑制,例如本研究中使用的5N-Al絲材料。
本研究通過表征高純鋁、鎳和銅的斷裂,研究了這些不同破壞機制之間的相互作用,探究了這些材料從擴散頸形成到最終試樣分離的整個破壞過程。主要成果如下:
(1)失效過程經常涉及到若干機制的連續發展。當這種情況發生時,一種失效機制通常會促進隨后出現的機制。
(2)在破壞前的變形過程中發生的微觀組織演變可以消除或產生材料中的空洞形核位點。這可以顯著影響不同失效機制之間的競爭。
(3)間隙剪切與空隙板的競爭取決于應變硬化能力,低應變硬化能力有利于間隙剪切,高應變硬化能力有利于空隙板。
(4)據推測,在剪切主導載荷下,應變到破壞的差異不僅是由于應變測量的空間分辨率和破壞定義的差異,而且還由于特定材料/條件下主導機制的差異以及可能導致破壞的多種機制的代表性不足。
免責聲明:本網站所轉載的文字、圖片與視頻資料版權歸原創作者所有,如果涉及侵權,請第一時間聯系本網刪除。
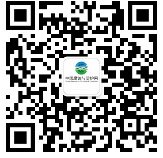
官方微信
《腐蝕與防護網電子期刊》征訂啟事
- 投稿聯系:編輯部
- 電話:010-62316606
- 郵箱:fsfhzy666@163.com
- 腐蝕與防護網官方QQ群:140808414