摘要
利用附著力測試、吸水率測試和電化學阻抗譜測試等手段,研究了淡水艙涂層在反滲透水、調質水、自來水等淡水以及鹽水中的腐蝕失效行為。結果表明,自來水比鹽水具有更快的滲透速度,導致涂層在淡水中會優先失效。淡水艙涂層在反滲透水、調質水和飲用水3種淡水中的腐蝕失效歷程相同,根據電化學阻抗譜的變化特征可分為3個階段:水的快速滲透、涂層/金屬界面金屬基體的腐蝕和涂層中顏填料對金屬的緩蝕。
關鍵詞: 涂層; 淡水; 腐蝕; 電化學阻抗譜
環氧樹脂涂層因具有強的附著力、良好的力學性能和優異的耐腐蝕性能被廣泛應用于金屬表面的防護,環氧涂層的失效與外界離子的傳輸[1,2]、涂層從金屬界面的剝離[3-5]密切相關,在一定程度上講,涂層失效的本質是外界腐蝕介質通過涂層內部滲入到涂層/金屬基體界面而使涂層喪失保護作用的過程。因此,涂層/金屬界面的結合以及涂層對外界腐蝕介質的抵抗能力成為了決定環氧涂層壽命的兩個重要因素,對于環氧涂層界面結合和致密性的改性[6-9]、環氧涂層的失效評價[10-16]引起了廣泛關注。以上對于環氧涂層的研究所涉及的腐蝕介質多為含Cl-的鹽水環境,對于環氧涂層在淡水環境中的腐蝕失效報道較少。
淡水艙涂層是保障海上淡水飲用安全和保持船體免受腐蝕的重要載體[17],了解不同淡水環境對涂層性能的影響對于淡水艙涂層的選擇和設計具有重要的意義。本文將主要圍繞涂層與金屬基體的附著性能、水的傳輸行為和涂層致密性3個方面,對比研究淡水艙涂層在鹽水和淡水中的腐蝕行為差異以及涂層在反滲透水、調質水和飲用水3種淡水環境中的腐蝕失效過程。
1 實驗方法
本工作研究對象為一種國產的無溶劑型環氧涂層,主要用于淡水艙的涂覆,實驗基材為Q235鋼板,表面經噴砂處理達到Sa2.5級,涂層噴涂厚度80~95 μm。所選擇的溶液介質包括利用海水淡化技術處理得到的反滲透二級產水 (ROW),通過在反滲透水中加入50 mg/L MgCl2、35 mg/L CaCl2和90 mg/L NaHCO3所得的調質水 (CW),海水淡化處理后兩種淡水中Cl-含量均小于0.02 mg/L,具體的性質如表1所示。除此之外,還引入了沈陽市的飲用水 (DW) 和3.5% (質量分數) NaCl (SW) 作為對比。
表1 兩種淡水的性質
根據GB/T 5210-2006,采用PosiTest?AT-A全自動數字顯示拉拔式附著力測試儀對在不同水溶液中分別浸泡0、240、480、720和1200 h的涂層樣品進行了附著力測試,每個時間點測量6次,取6次測試的平均值作為該時間點的附著力值。
為了測試不同的水溶液介質在涂層中的傳輸行為,需制備涂層的自由膜樣品,具體過程為將涂料均勻噴涂到硅膠板上,涂層厚度為約100 μm,涂層表干后將其從硅膠板上手工剝離,待其實干后,用裁刀將涂層裁成20 mm×20 mm的薄片,即為涂層自由膜樣品,并記錄每個樣品的原始質量m0,涂層樣品在浸泡t時刻的吸水率利用以下公式計算可得:
其中,Qt為涂層樣品浸泡t時刻的吸水率,mt和m0為涂層樣品浸泡t時刻及浸泡前的質量。
利用VersaSTAT V3F電化學工作站對浸泡不同時間的涂層樣品進行了開路電位 (OCP) 和電化學阻抗譜 (EIS) 測試,其中待測樣品為工作電極,鉑片為對電極,飽和甘汞電極為參比電極。電化學阻抗譜測試前先進行10 min的開路電位掃描,待電位穩定后進行測試,頻率測試范圍105~10-2 Hz,正弦波擾動振幅為20 mV。
2 結果與討論
2.1 淡水艙涂層在鹽水和淡水中的失效機制
2.1.1 涂層附著性能
淡水艙涂層與金屬基體界面的濕態附著力能直觀地體現涂層在實際服役過程中的附著性能,利用拉開法分別測試了淡水艙涂層在鹽水和飲用水中分別浸泡0、240、480、720和1200 h后的附著力,得到淡水艙涂層濕態附著力隨時間的變化,如圖1所示。可以看出,無論是在鹽水中還是飲用水中,淡水艙涂層隨浸泡時間的增加,附著力均沒有下降的趨勢。淡水艙涂層在兩種溶液中濕態附著力隨時間的變化趨勢不同,在鹽水中,其附著力表現為波浪式上升的趨勢,1200 h浸泡后已由初始的約5 MPa增加到約8 MPa,在飲用水中,其附著力表現為先增加后降低的變化特征,1200 h浸泡后附著力與初始值基本一致。
圖1 淡水艙涂層在鹽水和飲用水中濕態附著力隨時間的變化
在鹽水和飲用水環境下淡水艙涂層浸泡不同時間拉拔測試后的典型宏觀形貌如圖2所示。由圖2a可知,在鹽水中浸泡240 h后,金屬基體表面已見明顯腐蝕點,隨著浸泡時間的增加,基體表面腐蝕區域增多。從斷裂形式上分析,浸泡240和480 h后,涂層為混合型斷裂,表現為金屬基體表面仍有一部分涂層殘留,浸泡720和1200 h后斷裂形式表現為完全斷裂。與在鹽水中的情況相似,淡水艙涂層在浸泡240 h后,金屬基體表面已產生肉眼可見腐蝕點,隨著浸泡時間的增加,銹蝕區域的數量和面積不斷增多,且比在鹽水中的銹蝕更嚴重。從斷裂形式上判斷,淡水艙涂層在飲用水中均為完全斷裂,金屬基體表面絕大部分涂層已從金屬表面剝離。
圖2 鹽水和飲用水浸泡環境下拉拔測試后淡水艙涂層典型的宏觀形貌
2.1.2 介質的水傳輸性能
淡水艙涂層在鹽水和飲用水中的水傳輸動力學曲線如圖3所示。從圖中可以明顯看出,淡水艙涂層在兩種溶液中的水傳輸過程均可分為兩個階段:吸收階段和飽和階段,且達到飽和階段的時間都在50 h左右。所不同的是,同一時間節點淡水艙涂層在飲用水中具有更高的吸水率,飽和吸水率高達1.3%,明顯高于鹽水中的飽和吸水率1%。由此說明,飲用水較鹽水具有更高的水滲透壓,更容易通過涂層滲透到基體,這也就解釋了為什么淡水艙涂層在飲用水中更容易銹蝕 (圖2)。
圖3 淡水艙涂層在鹽水和飲用水中的水傳輸動力學曲線
2.1.3 涂層致密性
涂層的致密性與涂層的電化學性質密切相關,可通過研究涂層的電化學失效歷程監測涂層致密性的變化。淡水艙涂層在鹽水和飲用水中開路電位隨時間的變化如圖4所示,可以看出,淡水艙涂層在兩種溶液中開路電位的變化趨勢完全不同,在鹽水中的開路電位變化可分為3個階段:第1階段電位快速降低階段,電位由開始時的0.15 V快速下降至96 h的-0.33 V,第2階段電位波動階段,由96 h的-0.33 V升高至480 h的-0.12 V而后迅速降低至600 h的-0.57 V,第3階段電位平穩階段,600~1200 h電位穩定在-0.6 V左右。為了便于比較,淡水艙涂層在飲用水中的開路電位也可分為3個階段:第1階段電位下降階段,0~96 h,開路電位由-0.05 V降至-0.07 V,在96~600 h電位快速上升階段,由-0.07 V升高至-0.03 V,96~1200 h電位波動上升階段,由-0.03 V波浪式上升至-0.02 V。
圖4 淡水艙涂層在鹽水和飲用水開路電位隨時間的變化
根據淡水艙涂層在鹽水中開路電位的變化特征,淡水艙涂層在3個階段的電化學阻抗譜如圖5所示。從圖5中可以看出,淡水艙涂層在0~96 h電化學阻抗譜呈現容抗弧的特征,且容抗弧的半徑隨著浸泡時間的增加迅速減小 (圖5a),電化學阻抗模值由0 h的1.1×1011降至96 h的2.9×109 Ω·cm2,降低了約2個數量級 (圖5b),高頻相位角接近90°,低頻相位角隨著浸泡時間的增加不斷降低 (圖5c)。在96~600 h,淡水艙涂層阻抗譜依然表現出容抗弧的特征,且雙容抗弧的特征愈發明顯,容抗弧的半徑隨浸泡時間的增加繼續降低 (圖5d),低頻阻抗模值由96 h的2.9×109 Ω·cm2降低到600 h的2.7×108 Ω·cm2,阻抗模值再次降低1個數量級 (圖5e),隨著頻率的降低,相位角不斷降低 (圖5f)。在600~1200 h,淡水艙涂層阻抗譜表現出高頻容抗和低頻擴散的特征 (圖5g),阻抗模值和相位角維持在一個相對穩定的狀態 (圖5h和i)。
圖5 淡水艙涂層在鹽水中浸泡不同時間的電化學阻抗譜
淡水艙涂層在飲用水中3個階段電化學阻抗譜如圖6所示。淡水艙涂層在0~96 h電化學阻抗譜呈現容抗弧的特征,且容抗弧的半徑隨著浸泡時間的增加迅速減小 (圖6a),電化學阻抗模值由0 h的8.8×1010 Ω·cm2降至96 h的9.8×109 Ω·cm2,電化學阻抗模值降低了約1個數量級 (圖6b),高頻相位角接近90°,低頻相位角隨著浸泡時間的增加不斷降低 (圖6c),這與其在鹽水中0~96 h階段的變化特征相似。在96~600 h,淡水艙涂層阻抗譜依然表現出容抗弧的特征,容抗弧的半徑隨浸泡時間的增加繼續降低 (圖6d),低頻阻抗模值呈現緩慢下降的趨勢,由96 h的9.8×109 Ω·cm2降低到600 h的3.5×109 Ω·cm2,降低了2倍多 (圖6e),隨著頻率的降低,相位角不斷降低,相位角的形狀已基本不變 (圖6f),這與其在鹽水中96~600 h的變化特征保持一致。在600~1200 h,淡水艙涂層阻抗譜依然表現出容抗弧的特征,且容抗弧的半徑大小和低頻阻抗模值的變化趨勢與其開路電位的變化相似,呈現波動式上升的趨勢 (圖6g和h),相位角的形狀隨浸泡時間的增加已基本不再變化 (圖6i)。
圖6 淡水艙涂層在飲用水中浸泡不同時間的電化學阻抗譜
淡水艙涂層在鹽水和飲用水中電化學阻抗譜低頻模值隨時間的變化如圖7所示。可以看出,在涂層失效歷程的0~96 h階段,淡水艙涂層在鹽水和飲用水中的阻抗模值隨浸泡時間的增加均表現為快速降低的趨勢,由1011降低到1010 Ω·cm2,降低了約1個數量級,但涂層在鹽水中的低頻阻抗模值要高于其在飲用水中的值,這是由于飲用水在涂層中的傳輸速度要明顯高于鹽水 (圖3),迅速破壞了涂層的致密性。隨著浸泡時間的增加,涂層失效進入到96~600 h階段,淡水艙涂層在鹽水中電化學阻抗譜的低頻模值持續降低,降低約1.5個數量級,而其在飲用水中電化學阻抗譜的低頻模值緩慢降低,維持在109 Ω·cm2這個數量級,比其在鹽水中的模值高出1個數量級,造成這種差異的主要原因是此時鹽水和飲用水均已滲入到涂層/金屬界面,所不同的是鹽水對金屬基體的破壞速度明顯高于飲用水,使得涂層體系的阻抗模值持續降低。涂層失效進入到600~1200 h階段,淡水艙涂層在鹽水中的低頻模值已趨于平穩,保持在108 Ω·cm2這個數量級,而其在飲用水中的低頻模值出現緩慢上升而后趨于穩定的變化特征,穩定在1010 Ω·cm2,導致最終淡水艙涂層在飲用水中的低頻阻抗模值比其在鹽水中高出約1.5個數量級。
圖7 淡水艙涂層在鹽水和飲用水中電化學阻抗譜低頻模值隨時間的變化
2.2 淡水艙涂層在不同淡水中的失效機制
為了研究淡水艙涂層在不同淡水中的失效機制,選擇了經海水淡化處理的反滲透水、在反滲透水基礎上通過調整離子濃度得到的調質水以及飲用水3種淡水。淡水艙涂層在飲用水中的失效歷程已在上節論述,這里不再重復贅述,著重介紹其在反滲透水和調質水中的失效機理。
2.2.1 淡水艙涂層在不同淡水中的附著性能
分別測試了淡水艙涂層在3種淡水中浸泡不同時間后的涂層附著力,測試結果如圖8所示。可以看出,第一,淡水艙涂層經不同淡水浸泡后附著力并無明顯降低的現象,相反,經過1200 h的浸泡,其在反滲透水和調質水中的附著力反而出現了上升的現象,這可能與涂層中的防腐助劑和防銹顏料有關;第二,淡水艙涂層在不同淡水中附著力隨浸泡時間的增加并無明顯的變化規律。
圖8 淡水艙涂層在不同淡水中附著力隨浸泡時間的變化
淡水艙涂層在反滲透水和調質水中浸泡不同時間附著力測試后的宏觀形貌分別如圖9所示。從圖中可以看出,對于兩種不同的淡水,在浸泡240 h后,金屬基體表面均可見明顯的銹點,說明此時兩種水介質均已滲透涂層到達涂層/金屬界面,造成了金屬基體的腐蝕。此時,金屬基體上還有部分涂層殘留,隨著浸泡時間的增加,涂層已基本完全被拔開,金屬基體表面銹蝕程度增加。
圖9 淡水艙涂層在反滲透水和調制水中浸泡不同時間附著力測試后的宏觀形貌
2.2.2 淡水艙涂層在不同淡水中的水傳輸性能
淡水艙涂層在3種淡水環境中的水傳輸動力學曲線如圖10所示。可見,涂層在3種淡水中的水傳輸過程均可分為兩個階段:吸收階段和飽和階段,且達到飽和階段的時間都在50 h左右。所不同的是,調質水和飲用水中具有更高的吸水率,飽和吸水率高達1.3%,稍高于反滲透水中的飽和吸水率1.2%。
圖10 淡水艙涂層在3種不同淡水環境的水傳輸動力學曲線
2.2.3 淡水艙涂層在不同淡水中的致密性能
淡水艙涂層在3種淡水環境中開路電位隨時間的變化如圖11所示。可以看出,涂層在3種淡水環境中開路電位隨時間的變化特征基本一致,均表現為波動式上升的趨勢。所不同的是,涂層在反滲透水中的開路電位始終最高,其次是調質水,最低的為飲用水。為了方便和飲用水做對比,同樣將涂層在反滲透水和調質水中的失效歷程分成0~96,96~600和600~1200 h 3個階段。
圖11 淡水艙涂層在3種淡水環境中開路電位隨浸泡時間的變化
淡水艙涂層在反滲透水中3個階段的電化學阻抗譜如圖12所示。淡水艙涂層在0~96 h電化學阻抗譜呈現容抗弧的特征,且容抗弧的半徑隨著浸泡時間的增加迅速減小 (圖12a),電化學阻抗模值由0 h的9.3×1010 Ω·cm2降至96 h的1.0×1010 Ω·cm2,電化學阻抗模值降低了約1個數量級 (圖12b),高頻相位角接近90°,低頻相位角隨著浸泡時間的增加不斷降低 (圖12c),整體表現出兩個時間常數的特征。在96~600 h,淡水艙涂層阻抗譜依然表現出容抗弧的特征,容抗弧的半徑隨浸泡時間的增加繼續降低 (圖12d),低頻阻抗模值呈現緩慢下降的趨勢,由96 h的1.0×1010 Ω·cm2降低到600 h的4.6×109 Ω·cm2,降低了1倍多 (圖12e),隨著頻率的降低,相位角不斷降低,但隨時間的增加,相位角的形狀已基本不變 (圖12f),依然表現出兩個時間常數的特征。在600~1200 h,淡水艙涂層阻抗譜依然表現出容抗弧的特征,且容抗弧的半徑大小和低頻阻抗模值的變化趨勢與其開路電位的變化相似,呈現波動式上升的趨勢 (圖12g和h),相位角的形狀隨浸泡時間的增加已基本不再變化 (圖12i)。
圖12 淡水艙涂層在反滲透水中浸泡不同時間的電化學阻抗譜
淡水艙涂層在調質水中3個階段的電化學阻抗譜如圖13所示。淡水艙涂層在0~96 h電化學阻抗譜呈現容抗弧的特征,且容抗弧的半徑隨著浸泡時間的增加迅速減小 (圖13a),低頻阻抗模值由0 h的9.1×1010 Ω·cm2降至96 h的1.1×1010 Ω·cm2,降低了約1個數量級 (圖13b),高頻相位角接近90°,低頻相位角隨著浸泡時間的增加不斷降低 (圖13c),整體表現出兩個時間常數的特征。在96~600 h,淡水艙涂層阻抗譜依然表現出容抗弧的特征,容抗弧的半徑隨浸泡時間的增加繼續降低 (圖13d),低頻阻抗模值呈現緩慢下降的趨勢,由96 h的1.1×1010 Ω·cm2降低到600 h的4.8×109 Ω·cm2,降低了1倍多 (圖13e),隨著頻率的降低,相位角不斷降低,但隨時間的增加,相位角的形狀已基本不變 (圖13f),依然表現出兩個時間常數的特征。在600~1200 h,淡水艙涂層阻抗譜容抗弧的特征依然沒有改變,且容抗弧的半徑大小和低頻阻抗模值的變化趨勢與其開路電位的變化相似,呈現波動式上升的趨勢 (圖13g,h),相位角的形狀隨浸泡時間的增加已基本不再變化 (圖13i)。
圖13 淡水艙涂層在調質水中浸泡不同時間的電化學阻抗譜
綜合以上分析可知,淡水艙涂層在反滲透水、調質水和飲用水3種淡水環境中表現出相同的腐蝕失效機制,腐蝕失效歷程均可分成3個階段,每個階段低頻阻抗模值隨時間的變化如圖14所示。第1階段,隨著水介質的快速滲透,涂層的阻抗模值迅速降低,由數量級1011 Ω·cm2降至1010 Ω·cm2,降低幅度達1個數量級,其中飲用水的阻抗模值要低于反滲透水和調質水,如圖14a所示,主要原因是3種淡水中飲用水在涂層中的擴散速度最快 (圖10)。第2階段,水質已滲透到涂層/金屬界面,并造成了金屬基體的腐蝕 (圖2b、圖9),導致涂層的阻抗模值繼續降低,降低的幅度較第1階段有所減小,600 h過后阻抗模值降低為96 h的一半,維持在這個109 Ω·cm2數量級,并且飲用水中的阻抗模值依然最小,如圖14b所示。第3階段,在涂層中防腐助劑、防銹顏填料等的綜合作用下,涂層的阻抗模值再次上升到第2階段開始時的水平,如圖14c所示。
圖14 淡水艙涂層腐蝕失效過程中低頻阻抗模值隨時間的的變化
3 結論
(1) 淡水艙涂層在鹽水和飲用水中的附著力隨著浸泡時間的增加均沒有降低的趨勢,淡水艙涂層中飲用水比鹽水具有更快的滲透速度,導致涂層在淡水中會優先失效,隨著腐蝕介質不斷滲透到涂層/金屬界面,由于鹽水比飲用水對金屬基體的腐蝕性更強,導致最終涂層在飲用水中的阻抗模值明顯高于其在鹽水中的值。
(2) 涂層在反滲透水、調質水和飲用水3種淡水中的腐蝕失效過程相同,電化學阻抗譜特征上可分為明顯的3個階段:阻抗譜的快速下降,緩慢下降和上升階段,造成以上特征的原因分別是水的快速滲透、涂層/金屬界面的腐蝕和防銹顏填料的緩蝕。
參考文獻
[1]
Dong Y H, Zhou Q.
Relationship between ion transport and the failure behavior of epoxy resin coatings
[J]. Corros. Sci., 2014, 78: 22
[本文引用: 1]
[2]
Posner R, Marazita M, Amthor S, et al.
Influence of interface chemistry and network density on interfacial ion transport kinetics for styrene/acrylate copolymer coated zinc and iron substrates
[J]. Corros. Sci., 2010, 52: 754
[本文引用: 1]
[3]
Bi H C, Sykes J.
Cathodic delamination of unpigmented and pigmented epoxy coatings from mild steel
[J]. Prog. Org. Coat., 2016, 90: 114
[本文引用: 1]
[4]
Sørensen P A, Dam-Johansen K, Weinell C E, et al.
Cathodic delamination: Quantification of ionic transport rates along coating-steel interfaces
[J]. Prog. Org. Coat., 2010, 67: 107
[5]
Khun N W, Frankel G S.
Effects of surface roughness, texture and polymer degradation on cathodic delamination of epoxy coated steel samples
[J]. Corros. Sci., 2013, 67: 152
[本文引用: 1]
[6]
Shi C, Shao Y W, Xiong Y, et al.
Influence of silane coupling agent modified zinc phosphate on anticorrosion property of epoxy coating
[J]. J. Chin. Soc. Corros. Prot., 2020, 40: 38
[本文引用: 1]
師超, 邵亞薇, 熊義等.
硅烷偶聯劑改性磷酸鋅對環氧涂層防腐性能的影響
[J]. 中國腐蝕與防護學報, 2020, 40: 38
[本文引用: 1]
[7]
Liu X L, Shao Y W, Zhang Y J, et al.
Using high-temperature mechanochemistry treatment to modify iron oxide and improve the corrosion performance of epoxy coating-I. High-temperature ball milling treatment
[J]. Corros. Sci., 2015, 90: 451
[8]
Liu X L, Shao Y W, Zhang Y J, et al.
Using high-temperature mechanochemistry treatment to modify iron oxide and improve the corrosion performance of epoxy coating-II. Effect of grinding temperature
[J]. Corros. Sci., 2015, 90: 463
[9]
Deyab M A, Ouarsal R, Al-Sabagh A M, et al.
Enhancement of corrosion protection performance of epoxy coating by introducing new hydrogenphosphate compound
[J]. Prog. Org. Coat., 2017, 107: 37
[本文引用: 1]
[10]
Montazeri S, Ranjbar Z, Rastegar S.
A study on effects of viscoelastic properties on protective performance of epoxy coatings using EIS
[J]. Surf. Coat. Technol., 2017, 111: 248
[本文引用: 1]
[11]
Creus J, Mazille H, Idrissi H.
Porosity evaluation of protective coatings onto steel, through electrochemical techniques
[J]. Surf. Coat. Technol., 2000, 130: 224
[12]
Upadhyay V, Battocchi D.
Localized electrochemical characterization of organic coatings: A brief review
[J]. Prog. Org. Coat., 2016, 99: 365
[13]
Posner R, Wapner K, Amthor S, et al.
Electrochemical investigation of the coating/substrate interface stability for styrene/acrylate copolymer ?lms applied on iron
[J]. Corros. Sci., 2010, 52: 37
[14]
Nazarov A, Le Bozec N, Thierry D.
Assessment of steel corrosion and deadhesion of epoxy barrier paint by scanning Kelvin probe
[J]. Prog. Org. Coat., 2018, 114: 123
[15]
Cambier S M, Posner R, Frankel G S.
Coating and interface degradation of coated steel, Part 1: Field exposure
[J]. Electrochim. Acta, 2014, 13: 30
[16]
Cambier S M, Frankel G S.
Coating and interface degradation of coated steel, Part 2: accelerated laboratory tests
[J]. Electrochim. Acta, 2014, 136: 442
[本文引用: 1]
[17]
Shi Y, Fang Q, Guo C Q, et al.
Preparation of environmentally friendly ship fresh water tank coatings and study on its properties
[J]. China Coat., 2016, 31(10): 29
[本文引用: 1]
石勇, 方倩, 郭常青等.
環境友好型長壽命淡水艙涂料的制備及性能研究
[J]. 中國涂料, 2016, 31(10): 29
[本文引用: 1]
免責聲明:本網站所轉載的文字、圖片與視頻資料版權歸原創作者所有,如果涉及侵權,請第一時間聯系本網刪除。
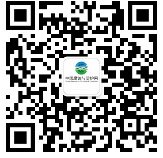
官方微信
《中國腐蝕與防護網電子期刊》征訂啟事
- 投稿聯系:編輯部
- 電話:010-62316606-806
- 郵箱:fsfhzy666@163.com
- 中國腐蝕與防護網官方QQ群:140808414